GALVANİZ
I. BÖLÜM
GALVANİZİN TANIMI VE TARİHÇESİ
1.1. GALVANİZİN TANIMI
Galvaniz işlemi elektrik akımı kullanılarak bir metalin üzerine daha kıymetli bir metalin kaplanması işlemidir. Galvaniz metali korozyona karşı korur ve metalin görünüşünü güzelleştirerek değerinin artmasını sağlar. Kuyumculukta değerli yarı değerli metaller (altın, gümüş v.s) için kullanılır.
Galvaniz modern galvano teknik “elektrolitik yolla” metal yüzey kaplama olarak ta adlandırılır. Galvaniz elektrolitik olarak metalik bir parçanın başka bir metal tabakasıyla kaplanmasıdır. Genelde elektroliz ya da kimyasal yolla kaplamacılık yapılır. Elektroliz kaplama da bir elektrolit içine iki elektrot daldırılıp, bu hücreye dıştan bir akım uygulayarak elektrotlarda kimyasal reaksiyonlar meydana getirilmesi olayıdır. Kuyumculukta bu yöntem tercih edilir.
1.2. GALVANİZİN TARİHÇESİ
Galvaniz metalleri korozyona karşı korur, metalin dayanıklılığını artırır ve değerinin artmasını sağlar. Galvaniz konusunda ilk çalışmaları Luigi Galvani yapmıştır.
Luigi Galvani, araştırmaları sırasında kurbağa sinir ve kas sistemi üzerinde deney yaparken metal keskinin cansız kurbağaya dokunduğunda kurbağanın hareket ettiğini görmüştür.O anda metalin canlılar üzerinde oluşturduğu elektrokimyasal bağlantıyı keşfedilmiştir.Bu fikir üzerine çalışmalarını yoğunlaştırıp bu konuda yaptığı araştırmaları 1791 yılında derleyerek yayınlamıştır.Bilim dünyasında bu araştırma büyük tartışmalara sebep olmuştur.Volta bu bulguya karşı fikir ortaya sürmüştür.O bunun bir metalik ark dan kaynaklandığını düşünüyordu.Bu tartışmalar sonucu canlılara doğru akım verilerek elektro terapi yapılabilirliği araştırılmaya başlanmıştır.
Alesandro Volta (1745–1827) Galvani nin fikirlerinden ve çalışmalarından çok etkilenmiş ve farklı metallerin elektriksel ilişkilerinin olabileceği ve bu ilişkiden enerji üretilebileceği fikrini geliştirmiştir. Bu yönde yoğun çalışmalar yapıp çalışmalarının sonucunda bakır ve çinkonun elektrik ilişkisi sonucu ortaya çıkan enerjiyi keşfedip bunu paketlenebilir enerji (pil) haline dönüştürmek için çalışmalarına devam etmiştir ve 1799 yılında Volta nın galvanic esaslı pilleri Kraliyet Enstitüsü tarafından kabul edilmiştir (http://www.Marmaragalvaniz.com).
Humphry Davy (1778–1829) Voltanın deneyimlerinden yola çıkarak farklı kimyasal özelliğe sahip farklı metallerin reaksiyonları ve sonuçları üzerine çalışmalar yapmaya başlamıştır. Volta temelde farklı metallerin kontaklarından ortaya çıkan enerjiye yoğunlaşmıştır. Oysa farklı iki metalin birlikteliği bir kimyasal reaksiyon ortaya çıkarıyordu ve bu reaksiyon bir tür elektrokaplamaya neden oluyordu. Davy deneyler sonucu platin katotlu galvanic pillerle potasyum üretmiştir. Bu yolla bir metalin başka bir metalle kaplanabileceği fikrine sahip olunmuştur.
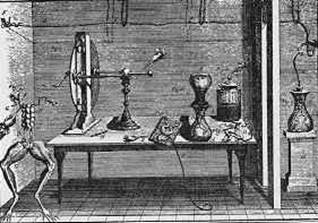
Resim 1: Galvaniz Deneyi
Humphry Davy ile birlikte çalışmalar yapan başka bir kişide İngiliz Kimyacı olan Michael Faraday, 1813 de yaptığı deneylerle yığın halindeki metallerin reaksiyonlarıyla oluşan doğru akımın kimyasal elektrolize bir yol izlediğini gözlemledi ve bunun bilimsel temellerini oturttu. Bu yasa Faraday Elektroliz Yasası olarak bilinir ve hala farklı metallerin korozyona uğramaları yoğunluk kaybetmeleri bu bilgiler ışığında yapılmaktadır.
Kayıtlara geçmiş ergimiş çinko ocağına demirin batırılması yöntemiyle yapılan ilk resmi çinko kaplama deneyi Fransız Kimyager P.J. Malouın tarafından 1742 yılında yapılmış ve Fransız Kraliyet Akademisine sunulmuştur.
1836 yılında ise bir başka Fransız kimyacı Stanilaus Tranquille Modeste Sorel çinko yoluyla demir kaplama ve % 9 sülfürik asit ile temizleme ve amonyum klorür ile yüzey hazırlama yöntemlerinin patentini almıştır. Bir yıl sonra 1837 yılında İngiliz Patent enstitüsü bu yöntemi onaylamıştır.1850 yılında İngiliz galvaniz endüstrisi 10.000 ton yıl galvanizleme gerçekleştirmiştir.
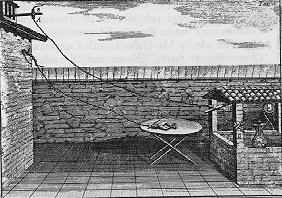
Resim 2: Galvaniz Deneyi
Galvaniz ilk çıktığı yıllarda büyük çelik yapıları korozyona karşı korumak için kullanılıyordu. Özellikle ulaşılması güç yerlerde yapılan çelikler enerji nakil hatları çeliğin kolay paslanması özelliğine karşı montaj öncesi kaplama ve uzun servis ömrü avantajıyla kullanılmaya başlandı. Zamanla teknolojik ilerlemelerle çeliğin kolay işlenebilirliği sayesinde dünyadaki çelik kullanımı arttıkça galvanizleme de paralel olarak artmıştır.
Yaklaşık 150 yıldır kompozisyonu galvanizlemeye uygun her türlü çelik artan oranda galvanizleniyor. Bugün pek çok sektör için galvanizleme vazgeçilmez olmuştur (http://www.Marmaragalvaniz.com).
II. BÖLÜM
GALVANİZ İŞLEMİNDE KULLANILAN YÖNTEMLER
VE GALVANİZ ÇEŞİTLERİ
2.1. GALVANİZ İŞLEMİNDE KULLANILAN YÖNTEMLER
Galvaniz işleminin yapımı sırasında kullanılan çeşitli yöntemler vardır. Bu yöntemleri kısaca tanımak gerekirse;
2.1.1. Elektroliz Yolu İle Kaplama (Electroplating)
Kaplanacak metal veya yüzeyi iletken hâle getirilmiş plâstik parça, kaplama için kullanılacak metalin tuzunun çözeltisi içerisinde katoda bağlanarak, metal katyonlarının, elektrik akımı geçirilerek kaplanacak yüzey üzerinde birikmesi ile gerçekleştirilir.
Yaklaşık 33 tane metal ile sulu çözeltilerinin elektrolizinden kaplama yapılabilir. Diğer metaller ile kaplama yapmak için erimiş tuzları veya organik elektrolitleri elektroliz edilir. Yaklaşık 15 metal ile olan kaplama ticarî maksatlıdır. Bunlardan bazıları: Bakır, gümüş, çinko, altın, platin, kadmiyum, kalay, kurşun, krom ve nikeldir.
Kuyumculukta üç elektroliz işlemi kullanılmaktadır.
Elektrolizin pürüzsüz yüzeyler elde etmek amacıyla mikro tepelerden metal çıkarılması için kullanıldığı elektrolitik parlatmadır.
Süsleme ya da koruma amacıyla, daha az soylu bir metal, hatta iletken olmayan bir metal üzerine kaplamayla (çöktürülerek) soylu metalden ince (birkaç mikron kalınlığında) bir tabakayla elektro kaplamadır.
Kalın bir metal tabakasının sonradan çıkarılacak ya da kalacak olan formlanmış bir şekil üzerine kaplandığı elektroformlamadır (Altın Takı Üretimi Teknik El Kitabı).
2.1.1.1. Elektroform
Kaplamaların yerini ve derecesini kontrol edilmesinin başlıca yolu, iyonların bu bölgelere çökelmesini engelleyecek şekilde yüzeyin bazı kısımlarının örtülmesidir. Bunun için çökelmeyi önleyen vernik, lake, selüloz kullanılır. Çökelmeyi önleyen bu maddelerin bazıları alkali koşullar bazıları ise asit koşullar için daha elverişlidir. Kullanılan maddelerin kaplama sonrası çıkarıla bilmeleri açısından farklılıklar gösterirler, bu açıdan en kolay çıkarılabilen kaplamalar lastik benzeri kaplamalardır.
Kaplama yapılacak heykelimsi nesneler elektroformlanırken nesne dışa doğru büyüdüğü için hassasiyet kaybı meydana gelir bunun için bazı nesneler içi boş mandrel kullanılarak daha hassas bir şekilde elektroformlanabilir. Mandrel modelin sonradan kendini taşıyabilmesine yetecek kadar kalın olan uygun kalıplanabilir bir malzeme ( kil, bal mumu )ile kaplanmasıyla oluşturulur. Daha sonra iki veya daha fazla kesit halinde modelden çıkartılarak içi boş bir model olarak yeniden bir araya getirilmelidir. Bu aşamada, kopya modelin iç kısmına anotlar ve elektrolit yerleştirilir ve kopya modelin hassas iç kısmına temas eden ilk kaplama katranı bu noktada içeri doğru kalınlaşarak büyümeye devam eden elektroformun hassas dış yüzünü oluşturur (Altın Takı Üretimi Teknik El Kitabı).
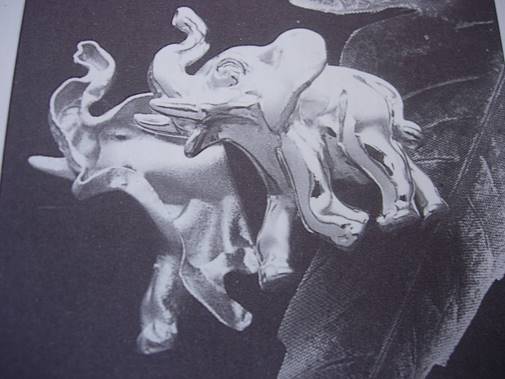
Resim 3: Elektroform İle Üretilmiş İçi Boş Takı
Elektroformlamada en önemli nokta kaplanacak yüzey alanının hesaplanmasıdır. Başlangıç alanı bilindikten sonra, elektro kaplamanın büyümesinden dolayı oluşan değişikliklerin hesaplanması zor değildir. Yüzey alanının hesaplanmasının amacı elektroformlana sırasında akım yoğunluğunun doğru bir şekilde ayarlanmasıdır. Akım yoğunluğu formlamanın başlangıcında düşük, sonunda yüksektir.
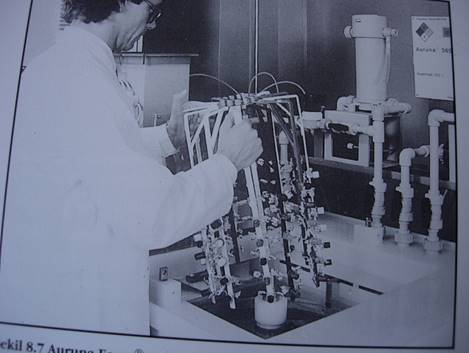
Resim4: Auruna Form Sistemi
2.1.1.2. Elektrokaplama (Electroplatıng)
Elektrokaplama da saf altını kaplamak ayarlı altını kaplamaktan daha kolaydır. Saf altına ince bir kat 14–22 ayar kaplama ile rengini orta sarıdan farklı bir renge hafifçe değiştirmek mümkündür. 9–14 ayar altının rengini de yüksek ayar ince bir kat kaplama ile değiştirmek mümkündür. Sadece saf altının kaplandığı yerde, kaplama 24 ayar olarak tanımlanır.
Elektrokaplama ile en düşük maliyetle iyi bir yüzey cilası elde edilir. Bunun için, en az kalınlıkta ama tatmin edici homojen bir rengi koruyacak iyi bir örtücü güç gerekir. İyi cilanın çoğunu, kaplamadan önce çok ince bir altın katmanından oluşturmak çoğu zaman daha ekonomiktir. Tipik cila öncesi, parlak nikel kaplamadır ve alt damarın rengi ve dokusu, altın kaplamanın görünüşünü özellikle sadece birkaç mikron kalınlığında ise, önemli ölçüde etkiler. Parlatılmamış ve doku kazandırılmamış alt katmanlar, aynı altın kaplama banyosunda yan yana kaplandığında birbirinden oldukça farklı görünürler.
Kaplama kalınlığı kontrolü kaliteli ama ekonomik altın kaplama için olmazsa olmaz koşuldur. Bir altın tabakası veya renklendirmesi 5–30 saniye içinde dökülmüş, bir milimetrenin 50–25 milyonda biri kadar olabilir ve genellikle kaplanmış gibi parlak görünür. Elektrokaplama olarak tanımlanması için, kalınlık 150/10–6 mm. üzerinde olmalıdır; kaplamanın kendi nitelikleri yüzeyin görüntüsünü belirler (Altın Takı Üretimi Teknik El Kitabı).
Elektrolit 24ct sarı Sarı Pembe Yeşil Beyaz
|
Altın g/l 1.25-2.0 1.25-2.0 1.25-2.0 1.25-2.0 0.4
|
Nikel g/l - 0.025 0.025 0.025 -
|
Bakır g/l - 0.13 1.1 - 2
|
Gümüş g/l - - - 0.05 -
|
Potasyum g/l 15 15 15 15 15
|
Siyanürg/l 7.5 7.5 2 2 -
|
Akım A/dm2 7.5 7.5 2 2 -
|
Sıcaklık 60-70 65-70 60-70 60-70 65-70
|
Tablo 1: Elektrokaplama Sistemleriyle İlgili Veriler.
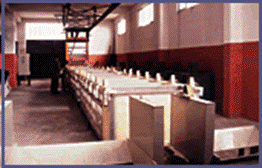
Resim 5: Elektro Galvaniz Kaplama Tesisi
2.1.1.3. Elektrolitik Parlatma
Elektrolitik parlatma sırasında, çıkıntılar aşındırılarak gitgide küçültülür ve aynı zamanda yüzey katmanları, alttaki katmanları silikleştirirler bu da parlatma etkisini artırır. Elektrolitik parlatma hızlıdır, iyi bir cilalama 5-10 dakika sürer.Bu işlemde elektro kaplamada kullanılanlara benzer ekipman kullanılır.Kullanılan solüsyon genellikle potasyum siyanürdür.İşlenecek parçalar, pozitif kutba bağlı olan anoda tutturulur; katot paslanmaz çelik veya çelik kaplama olabilir.Bu işlem aslında kaplama işleminin tersine çevrilmesidir. Akımın, çıkıntılara ulaştığı kolaylıkla oyuklara ulaşmasını önleyen elektrolitin iletkenliğinin ve hareketliliğinin düşük olmasından dolayı işlenecek parçanın çıkıntılarından altın çıkartılır. Sonuç olarak, yüzeyin pürüzlülüğü en az düzeye indirilir.
Elektrolitik parlatma uygulanmış bir yüzeyin görünüşü, mekanik olarak cilalanmış bir yüzeyin görünüşüyle pek aynı değildir. Aslında önceki yüzey kusurları elektrolitik parlatma ile abartılırken mekanik cilalama bunları bir şekilde gizler. Elektrolitik parlatma sonrasında mekanik cilalama yapılması, küçük gözenekleri kapayabilir (Altın Takı Üretimi Teknik El Kitabı).
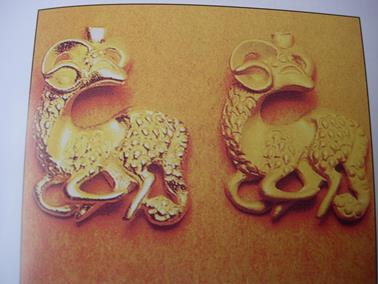
Resim 6:Elektrolitik Parlatmanın 14 Ayar Altın Döküm Üzerindeki Etkisi. Sağda
Elektrolitik Parlatma Olmadan Önce.
Elektrolitik parlatmanın 14 ayar döküm üzerindeki etkisi resimde görülmektedir. Genel görünüş, elle cilalama son işleme göre önemli derecede çok daha verimli bir şekilde parlatılmıştır fakat bu durumda küçük döküm kusurları çok daha barizdir. Elektrolitik parlatmada kullanılan akım yoğunlukları çoğunlukla kaplama için kullanılanlardan 10–100 kat yüksektir (A.T.Ü.T.EL KİTABI).
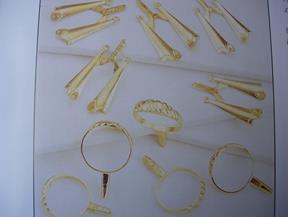
Resim7:Elektro Parlatma Uygulanan Takılar
2.1.2. Sıcak Daldırma
Sıcak daldırma galvaniz basit anlamda tasarımı ve kimyasal kompozisyonu galvanizlemeye uygun demir ve çelik ürünlerinin ergimiş çinko banyosuna daldırılmasıyla oluşan difüzyon sonucu meydana gelen metalik tepkimeyle oluşan kaplama yöntemidir.
Kaplanacak metal yüzeyi, temizlendikten sonra erimiş haldeki metale daldırılarak sathî difüzyon (yayınma) yoluyla kaplanması sağlanır. Bu amaçla kaplayıcı metal olarak çinko, kalay, kurşun ve alüminyum kullanılır.
Çelik, çinkoya daldırılarak galvanize edilir. Çinko yerine kalay da kullanılabilir. İnce demir saçlar kalaya daldırılarak teneke elde edilir. İşlem sırasında yüzeylerin oksitlenmesini önlemek için uygun flakslar, hidrojen veya soy gazlar kullanılarak yüzeylerin hava ile teması kesilir (http://www.galvaniz.com).
Resim 8: Sıcak Daldırma Galvaniz
2.1.3. Kimyasal İndirgeme Yoluyla Kaplama (Electroless)
Suda çözünen gümüş, altın ve bakır tuzlarının kuvvetli indirgeyici etkisi ile sulu ortamda indirgenmesi yoluyla cam (ayna yapımında olduğu gibi), plâstikler ve metaller kaplanabilmektedir.
2.1.4. Kimyasal Yer Değiştirme Yoluyla Kaplama
Cisimler, çözeltiden yer değiştirme yolu ile bakır, altın, gümüş ve kalay ile kaplanabilir. Kaplama kalınlığı çok incedir (2,5x10–6 mm kadar).
2.1.5. Püskürtme
Toz veya tel hâlinde uygun metal veya metal alaşımları bir tabancada eritilerek kaplanacak yüzeye püskürtülür. Püskürtme yoluyla kaplamada en çok kullanılan iki metal, çinko ve alüminyumdur. Metal püskürtme daha çok sıvı tanklarının, çelik yapıların yerinde kaplanması için kullanılır.
Püskürtme işleminde düşük erime noktasına sahip bir metal alaşımı eritilip bir tabanca aracılığıyla model üzerine tabaka oluşturacak şekilde püskürtülür. Kullanılan alaşımlar bizmut, kalay ve çinko gibi malzemeler içerirler. Çelik, alüminyum, bronz ve bakır gibi malzemelerin de kullanılabilmesine rağmen yüksek erime sıcaklıkları ve deformasyona sebep olmaları nedeniyle çok uygun değildirler. Bu işlem sprey boyama işlemine benzer şekilde yapılır.
Tabancada iki metal tel arasında oluşan arkla metal tel eritilir. Bu erimiş malzeme sıkıştırılmış hava kullanılarak model üzerine püskürtülür. Katılaşmadan sonra model üzerinde bir metal tabakası oluşturulmuş olur (atlas.cc.itu.edu.tr).
Püskürtme işleminin aşamaları
Bir model hazırlanır.
Model istenilen yüzey kalitesine getirilir.
Ejektör pimleri püskürtme yapılmadan önce yerleştirilmelidir. Bu pimler parçanın kalıp içerisinden kolayca alınmasını sağlayacaktır. Ayrıca, modelin kaplanmadan ayrılması için de kullanışlıdır. Çok fazla pim konulması kaplamayı güçleştirir.
Metal kaplama tabanca kullanılarak yaklaşık 2 mm kalınlığında kaplama uygulanır.
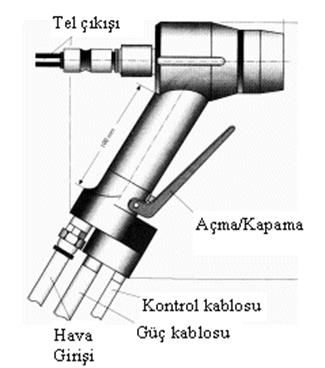
Resim 9: Metal Püskürtme Tabancası (Hek, MCP/TAFA 8850)
Model dikkatli bir şekilde kaplamadan ayrılarak alınır. Bu aşamada ejektör pimleri işin daha kolay yapılmasını sağlar.
Üretilecek parçanın malzemesine göre kaplama yüzeyi fırçalanmak suretiyle temizlenmelidir (atlas.cc.itu.edu.tr/~yagmur/makale/mak3/mak3.html).
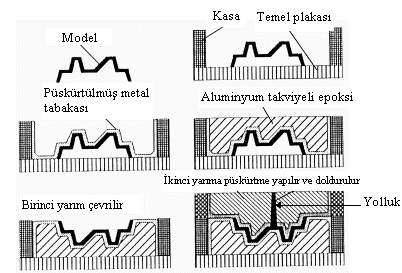
Resim 10:Metal Püskürtme İşleminin Aşamaları
2.1.6. Gaz Kaplama
Kaplama için kullanılacak metalin gaz hâlindeki bileşiği, genellikle karbonili, kaplanacak cisimde iken cisim ısıtılır. Sıcak yüzeyde gaz hâlindeki bileşikten metal atomu ayrılarak yüzeyde toplanır. Bu usulle daha çok nikel kaplama bazen de krom ve demir kaplama yapılabilmektedir.
2.1.7. Sementasyon veya Difizyon Kaplaması
Kaplanacak metal, kaplamada kullanılacak metalin tozu içine konularak ısıtılır. Ortamda oksitlenmeyi, hava ile teması önleyici maddeler, soy gazlar bulundurulur. Meselâ bir metalin alüminyum difüzyonu ile kaplanması demek olan kalorizasyon işleminde metal parça, içinde alüminyum tozu bulunan bir döner tanbur içerisine yerleştirilir. Demirin sementasyonunda sıcaklık 850°-950°C olur. Demirin çinko ile bu yoldan kaplanmasına şerardizasyon (shererdization) denir. Krom ile kaplama yapılırsa buna kromizasyon denir (www.bizimsahife.net).
2.1.8. Vakumda Yoğuşturma
Bu metotla döküm metaller ve plastikler de metalle kaplanır. Kaplama için kullanılacak metal, vakumda tungsten ısıtıcı ile ısıtılarak buharlaştırılır. Kaplanacak parçanın yüzeyi, temizlenmiş, düzeltilmiş ve cilâlanmış olarak metal buharı bulunan hücre içerisinde döndürülerek tutulur. Metal buharı soğuk parçanın yüzeyinde yoğuşur. Alüminyum, altın, gümüş ve buharlaştırılabilen diğer metaller bu amaçla kullanılır. Bu tür kaplamalar aşınmaya dayanıklı olmadığından, ayrıca bir lak ile kaplanır (www.bizimsahife.net).
2.1.9. Pin (vurma) Kaplama
Kaplanacak metal parçalar, kaplamada kullanılacak metal tozu ve aktive edici bir çözelti ile birlikte bir döner tambur içine konulur. Tambur içinde düşerek darbe etkisi yapan metal parçalar da vardır. Rondela (pul), çivi, zincir gibi küçük parçalar bu metotla çinko, pirinç ve kadmiyum ile kaplanır (http://www.bizimsahife.net).
2.2. GALVANİZ ÇEŞİTLERİ
Galvaniz birçok değerli, yarı değerli metal üzerine uygulanmaktadır. Bunlardan bazıları platin, altın, gümüş, bakır, pirinç gibi metallerdir. Galvaniz çeşitlerine kısaca bakacak olursak;
2.2.1. Platin Kaplama
Platin Esmer beyaz renkte, parlak bir madendir. Mıknatıslanabilir, büyük yoğunluğu ile yüzdürülerek zenginleştirilebilir, civa ile malgama yapmadığından altın ve gümüşten kolayca ayrılabilir. Platin en yüksek sıcaklıklarda bile havadan bozulmaz. Pek sert değildir, kolaylıkla levha, tel haline getirilebilir. Kimyasal simgesi Pt, atom numarası 78, Yoğunluğu 21,45 gr/cm3 , Atom ağırlığı 195,23 , Ergime noktası : 1778 °C ,
Platin tek tek hiç bir asitten etkilenmez, yalnızca kral suyunda (altın suyu) çözünür. Kuyumculukta platin, bakır(%10) veya rutenyum(%5), ya da iridyumla(%10) alaşım halinde kullanılır. Genellikle alyans veya yüksek değerli mücevherlerin yapımında platin tercih edilmektedir (tr.wikipedia.org).
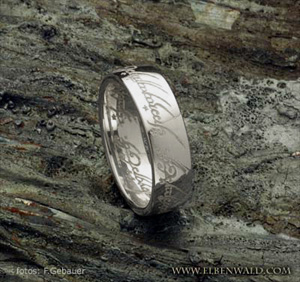
Resim 11: Platin Kaplama Alyans
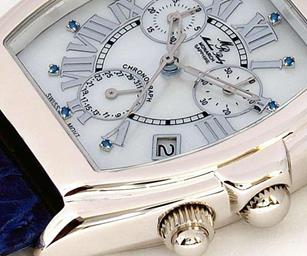
Resim 12: Kasa ve Düğmeleri Platin Kaplı Saat
2.2.2. Altın Kaplama
Altın parlak sarı renkte, nadir bulunan, çok değerli bir soy madendir. Çok yumuşaktır ve kolay işlenebilir. Isı ve elektrik iletkenliği mükemmeldir. Havadaki oksijenden ve sıcaklıktan etkilenmez. Civada çözünür. Asitlerden etkilenmezse de hidroklorik asit ve nitrik karışımı olan Altın Suyu' ndaki klorür etkisi ile erir.
Kimyasal simgesi Au, Atom numarası 79, Atom ağırlığı: 197,2, Ergime noktası 1063 °C, Kaynama noktası: 2800 °C, Isı iletkenliği : % 53,2, Elektrik iletkenliği % 65,46, Yoğunluğu: 19,7 gr/cm3 (tr.wikipedia.org).
Galvanizli altın kaplama kimyasal renklendirmenin yerini almıştır; daha geniş renk olasılıkları mümkün olup aynı anda parlak sonuç verebilmektedir. Günümüzde ise çoğunlukla kuyumculukta, elektronikte, dişçilikte, süslemecilikte, madalyon ve sikke basımında kullanılmaktadır. Kuyumculukta daha çok mücevherata, çizilmeye karşı mukavemetinden dolayı, kaplama yapılır. Kaplamanın kalınlığı ucuz mücevherde 0.000001 cm, daha iyilerinde 0.000005 cm kadar kalınlıkta olabilir. Kalın altın kaplama, bazı radar teçhizatında ve elektrik kontaklarında kullanılır. Altının pahalı olmasından dolayı, pratik olarak bütün altın kaplamalar seyreltik siyanür çözeltilerinden yapılır. Kalın altın kaplamalar, pirinç eşyanın seyreltik altın siyanür çözeltisine batırılmasıyla elde edilir (http://www.bizimsahife.net/Rehber Ansiklopedisi/index-70.htm).
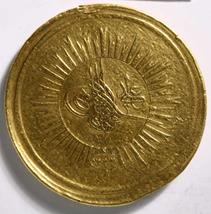
Resim 13: Altın Kaplama Sikke
Galvaniz yoluyla kaplanacak altının sertliği, nikel-potasyum siyanürü katılarak artırabilmektedir. Altının rengini bozmamak amacı ile belli bir yüzde aşılmamalıdır. Eklenecek nikel miktarı litre başına altın içeriğine bağlıdır. Litre başına 0,1 ila 3 g arasında değişmektedir. Arada bir, bu miktarın eklenmesi tekrarlanmalıdır. Eğer cerrahi ya da bilimsel aletlere korozyona karşı dayanıklılık kazandırmak ya da sadece dekoratif amaçla altın kaplanacaksa, 1000 milyemlik altın kullanılmalıdır. Bu durumda, kaplanacak nesne, adi metalden ise, parlak nikelajlı ara zemin oluşturulur. Dekoratif amaçlı kaplamaların kalınlıkları, mikronun onda ya da yüzde biri olmakta, başka bir deyişle dmz'ye 1,932 ile 0,193 santigram altın kaplanmalıdır. Bu kalınlıklar söz konusu olduğunda, altın kaplama herhangi ek bir işlem gerektirmeyecek kadar parlak olmalıdır. Diğer durumlarda, sertlik ve dayanıklılık gibi sınırlayıcı faktörler, neticede kaplanan altının rengini etkilemektedir.
Alın kaplama işleminde gümüş, bakır, pirinç, bronz gibi metallerin alt katmanlarının üzerine ince altın kaplama yapılarak özel tonlar elde edilebilir. Kaplamada altının kalınlığı belli bir değeri aştığında renk zeminden bağımsız hale gelir.
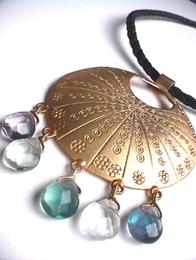
Resim 14: Gümüş Üzerine Altın Kaplama
Kaplama sırasında saf altınla gerçekleştirilen, sarı altın kaplamalarında akımı değiştirerek değişik renk tonlar elde edilebilir. Düşük akımlarda altın soluk sarı renktedir. Akım arttıkça renk daha sıcak hale gelmektedir. Akım yükseldikçe renk koyulaşır. Genelde altın kaplamalar kan taşı ile canlı hale getirilirdi. Şimdilerde parlak banyolar tercih edilmektedir. Küçük miktarlarda eklenen nikel parlaklığı sağlamakta kullanılmaktadır. Çözeltideki siyanürün etkisi ile eriyen nikel karbonat şeklinde eklenmektedir. Her seferinde çok az miktarda eklenmelidir.
Altın kaplamada kullanılan tuzlar şunlardır: % O 500'lük sarı altın klorürü, 520 %, koyu altın klorür; % 0683'lük altın ve potasyum siyanürü (KAu (CN) ), %o 565 milyemlik potasyum altın siyanürü (KAu(CN) ); 100 g/l ayarında siyanürlü altın sodyum (Na Au (CN )) %724 sıvı olarak bulunan altın sülfat. Son ikisi az kullanılmaktadır. Üreticiye bağlı ayarlarla, siyanür % 680 milyemlik olarak pazarlanmaktadır (VITIELLO,2006,s.383–386).
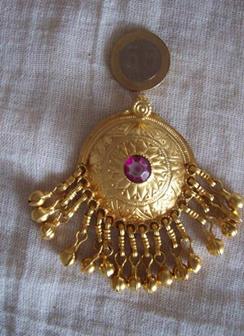
Resim 15: Altın Kaplama Kolye Ucu
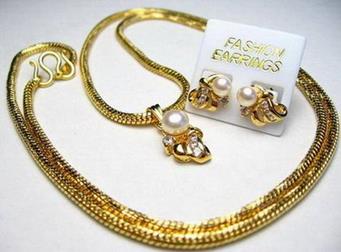
Resim 16: 18 Ayar Altın Kaplama Set
2.2.2.1. Nikel Altın Kaplama
Nikel/altın kaplama iki ayrı yöntemle yapılmaktadır. Bunlar elektroliz ve kimyasal kaplama yöntemleridir. Elektroliz yoluyla yapılan nikel/altın kaplama, yaklaşık olarak 10m. kalınlıkta nikel üzerine, yine yaklaşık olarak 2m. kalınlıkta altın kaplanmasıdır. Kimyasal nikel/altın kaplama yöntemine göre çevre şartlarına ve darbelere daha dayanıklı bir yapı sunan elektrolitik nikel/altın kaplama yöntemi, özellikle konnektör uçları gibi hareketli ve mekanik aşınmaya maruz bölgelere uygulanır. Dayanıklı bir yapıya sahip olan elektrolitik nikel/altın kaplama daha yüksek iletkenlik katsayısına sahip olmasına karşın, geniş yüzeylere uygulandığında kırılganlık özelliği de artmaktadır. Elektroliz yoluyla yapılan kaplamanın maliyeti de yüksek olmaktadır ( http://www.odevarsivi.TK/gonder.php ).
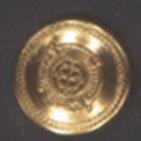
Resim 17: Nikel Altın Kaplama
2.2.2.2. 1000 Milyemlik Sıvı Altın Kaplaması
Kaplama işlemi 1 litre arı su içerisine altın ve potasyum çift siyanür 1,5 ila 3g potasyum siyanür 7,5 g potasyum fosfat 15 g konulur sıcaklık 60 ila 70 °C olmalı kaplama sırsında akım yoğunluğu 1 ila 4 A/dm2 bu işlemde çözülmeyen anottur.
2.2.2.3. Yeşil Kaplama
Yeşil kaplamada 1 litre su, içerisine altın ve potasyum çift siyanür 3g. Potasyum ve gümüş siyanür 0,5 g potasyum siyanür 7,5 g, gereken sıcaklık derecesi 55 ila 70 °C, akım yoğunluğu 0,5 ila 2,5 A/dm2 çözülmeyen anottur.
2.2.2.4. Pembe Kaplama
Pembe kaplama için 1 litre arı su, altın ve potasyum çift siyanür 1,5 g, bakır ve potasyum 3,5 g, nikel ve potasyum çift siyanür 1 g, potasyum siyanür 4 g, potasyum fosfat 15 g, 60 ya da 70 °C. sıcaklık ve 2,5 ila 4 A/dm2 akım yoğunluğu gereklidir (VITIELLO,2006,s.386).
2.2.2.5. Soluk Sarı Kaplama
Soluk sarı kaplama için altın ve potasyum siyanür 4 g/l, potasyum siyanür 4 g/l, potasyum demir siyanür 30 g/l, potasyum nikel siyanür 1,8 g/l, 60 ya da 70 °C. Sıcaklık ve 2 ila 4 A/dm2 akım yoğunluğu gereklidir.
2.2.2.6. Kırmızı Kaplama
Kırmızı kaplama için potasyum ve altın siyanür 4 g/l, potasyum siyanür 3 ila 7 g/l, Potasyum demir siyanür 30 g/l, Bakır siyanür 1,5 g/l, Potasyum nikel siyanür 2 g/l, 60 ya da 70 °C. Sıcaklık ve 3 ila 4 A/dm2 akım yoğunluğu gereklidir.
Altın kaplamaların rengi, pembeden ne kadar uzak ise, hava ile temasta buğulanmaya o kadar dayanıklı olmaktadırlar. Pembe renk sıcaklığın artması ile ya da akımın düşürülmesi ile çalkalamayla ya da potasyum siyanür eklenerek azaltılabilir (VITIELLO,2006,s.387).
2.2.2.7. Antik altın kaplama
Antik altın kaplama türü kabartma, telkari gibi nesnelerde tercih edilmelidir. Altın, kurşun, gümüş ya da kadmiyum katmanı oluşturularak parlak olmayan, koyu, isli bir görünüm elde edilir. Elde ince aşındırıcı ya da demir fırça ile işlenir. Sonuçta çukur bölgeler ile kabartma yüzeyler farklı ışıklandırma arz edeceklerdir. Küçük nesneler söz konusu olduğunda, çelik küreler içeren döner kazanlar da kullanılabilir.
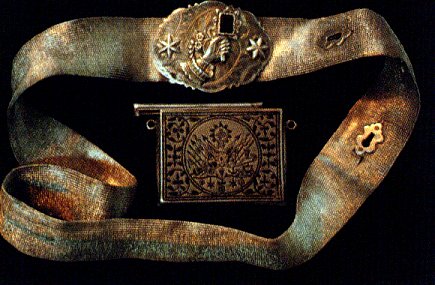
Resim 18: Antik Altın Kaplama Telkari (Trabzon)
İki ayrı çözelti tavsiye edilmektedir.Birinci çözelti için altın ve potasyum çift siyanür 4 ila 5 g., kadmiyum oksit 0,7 g., kurşun asetat 0,25 g., potasyum siyanür 10 g, su1 litre. İkinci çözelti için altın ve potasyum çift siyanür 3 ila 4 g., gümüş potasyum çift siyanür 1 ila 2 g., potasyum siyanür 7,5 G., kurşun asetat 7,5 G., su 1 litre gereklidir (VITIELLO,2006,s.387).
2.2.2.8. Vernikli Nesnelerin Altın Kaplaması
Vernikli nesnelerin altınla kaplanması halinde kolayca zarar verebileceğinden siyanürlü çözeltiler kullanılmamalıdır. Bu durumlarda çok eski olan bir demir siyanür çözeltisi ya da günümüze uyarlamış hali kullanılabilir.
Demir siyanür çözeltisi için altın klorür 2,65 g., potasyum-demir siyanür 15 g. sodyum karbonat 15 g., arı su 1 litre ,15 cm milyemlik elektrot aralığı için 2,1 V. her 5 cm için 0,1 V. 0,1 A/dm2 ve oda sıcaklığı. Günümüze uyarlanan çözelti için altın 8 g/litre (Altın ve potasyum siyanürü 12 g), sodyum nitrat 40 g\litre bu iki madde eritildiğinde, (40 g/l) oranında sitrik asit eklenir. Çevre sıcaklığında pH 3 ila 6Akım 0,5 1 A/dm2, anot platin, platin kaplı tan talyum ya da platin kaplı titanyumdur (VITIELLO,2006,s.388).
2.2.3. Gümüş Kaplama
İlk galvaniz işlemi "gümüş kaplama" dır. Kaplamada kullanılan çözeltiler siyanür ile eritilmiş gümüş içerir ayrıca belli bir miktarda potasyum ya da sodyum siyanürü içerirler. Bu serbest siyanür, iyi bir kaplamaya yol açmasının yanı sıra, Ag'nin anotta düzenli olarak erimesine de yardımcı olmaktadır.
Potasyum ve siyanür kullanılması halinde serbest siyanür 1 litre suda mevcut olan Ag miktarının % 60 olup, sodyum siyanür kullanılması halinde bu oran % 46'dır. Bu değerler Ag yönünden zengin olan banyolar için geçerli olup, asgari olarak kabul edilmelidir (VITIELLO,2006,s.377).
Gümüş kaplamada kaplanacak parçalar, anodu gümüş olan elektrolitik banyoda katoda bağlanırlar. Banyodaki elektrolit, sodyum arjantisiyanit, NaAg(CN)2 veya benzeri bir karmaşık gümüş tuzudur.
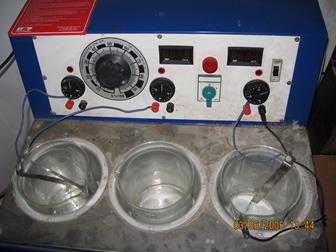
Resim 19: Kaplama Makinesi
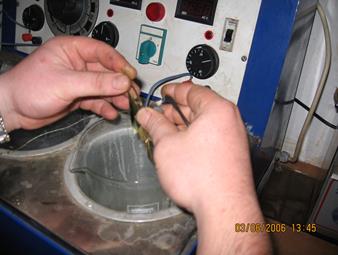
Resim 20: Kaplama İşlemi
Banyonun iletkenliğini artırmak amacı ile sodyum ya da potasyum karbona; eklenirdi. Ancak bu karbonatlar, hava ile siyanürün tepkimesinden zaten oluşmaktadır. Daha sonraları potasyum sodyuma göre daha iyi bir iletkenlik sağladığı ve karbonat alaşıma daha çok dayandığı gözlenmiştir. Günümüzde, çözeltinin hazırlanmasında. Ag siyanür, potasyum siyanür ve potasyum karbonat kullanılır.
Litre başına 90 gram Ag 'nin katılması ile banyo çözeltisinin üretim hız artmaktadır. Bu çözeltiler sıcak halde kullanılmakta, sürekli filtre edilmekte ve karıştırılmaktadır, ihtiyaca göre, sabit çözeltilerde, çevre sıcaklığında, duşu akımlarda geniş zaman sürelerinde işlem yapmak mümkündür. Her durumda gümüş kaplama banyolarının nüfuz etme gücü yüksektir (VITIELLO,2006,s.378).
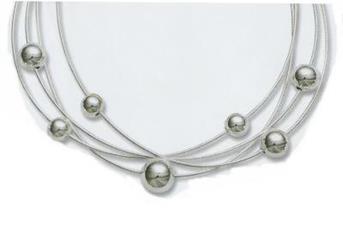
Resim 21: Gümüş Kaplama Kolye
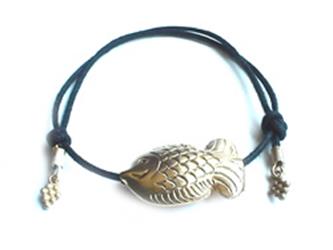
Resim 22: Gümüş Kaplama Bileklik
2.2.3.1. Gümüş Kaplamada Kalınlık ve Zaman
Bir nesnenin üzerine kaplanacak gümüş miktarı önceden tahmin edilebilmektedir. 800'lük gümüş de bu önemsizdir, çünkü alaşım ağırlığa göre satılmaktadır. Değişik ve daha ucuz metal, gümüş kaplanacağı zaman, her kalınlığın hem de ağırlığın bilinmesi kalitenin ve maliyetin tespitinde önemlidir.
Bu değerden yola çıkarak belli bir sürede oluşacak gümüş kaplamasının ağırlık ve kalınlığı hesaplanabilir. 0.0066 ile çarpıldığında bir dakika 4 ile çarpıldığına; bir saatteki gümüş ağırlığı hesaplanır. Kalınlık için dakika kat sayısı 0.634 saat katsayısı ise 38'dir (VITIELLO,2006,s.378).
2.2.4. Bakır Kaplama
Bakırın simgesi Cu dur. Kırmızı renklidir. Periyodik cetvelde 1B grubundadır. Hakiki metal olup, eksi değerleri yoktur. Atom numarası 29, Atom ağırlığı 63,546’dır. Erime noktası 1083°C, kaynama noktası 2595 oC’dir. Bakır cevherleri genel olarak üç sınıfa ayrılır: 1. Tabii bakır, 2. Sülfürlü cevherleri, 3. Oksitli.
Bakır kaplama, iki ayrı banyo ile gerçekleştirilebilir. Mavi renkte, bakır sülfat içerenler ve beyaz renkte bakır siyanür içerenler. Her ikisi de hızlı işlem meydana getirmektedir. Parlak ve düzgün yüzeyler elde edilebilir. Bu tür çözeltiler sadece ihtiyaç duyulduğunda kullanılmalıdır. Anot olarak piyasadaki sn saf bakır kullanılır. Elektrik iletmek için kullanılan bakır uygundur,
a) Asitli bakır kaplama: Eski, ancak etkili bir çözelti aşağıda verilmiştir.
Bakır sülfat 200 g
Derişik sülfürik asit 30 g
Su 1 lt
Hazırlanışı: Bakır sülfat sıcak suda eritilir ve karışım soğuduğunda sülfürik asit eklenir. Kaplar cam, moplen, polyester olabilir. Çözelti, ortam sıcaklığında, 2 A/dm2 azami akım yoğunluğu ile kullanılır. Bu şartlar dahilinde saate, 4.79 g yani 1/2 dm2'ye 22 mikronluk katman oluşturulabilir. Randıman % 100'e çok yakındır. Anot randımanı, katodunkinden fazla olup netice itibariyle çözelti bakırca zenginleşmeye asit yönünde fakirleşmeye yüz tutar (VITIELLO,2006,s.375).
Elektrotlar arasındaki mesafe 15 cm olan bir banyoda gerilim 0.5 İla1 V'dur. Akım fazla olduğunda, tozlu, pürüzlü bir kaplama elde edilir. Bu tür çözeltiler bakırın elektrolit rafine işleminde ve plastikte kullanılmaktadır, çünkü bakırın fiziki ve kimyasal özelliklerini değiştirmeden, herhangi bir kalınlıkta kaplama oluşturulabilmektedir, mg/litre mertebesinde destrin, jelâtin, fenolsofonik asit, tiare, arap yapışkanı gibi maddelerin eklenmesi ile bakır parlak ve pürüzsüz hale getirilebilir. Piyasada elekrolitik bakır, bu yöntemle elde edilmektedir,
b) Siyanürlü alkalin bakır kaplaması;
1 litre arı suya aşağıda ki maddeler eklenir.
Basit bakır siyanür 22 g
Sodyum siyanür 34 g
Sodyum hiiposüolfat 1 g
Sodyum karbonat 15 g
Soğuk halde suyun yarısında sodyum siyanür eritilir, bakır siyanür eklenir ve eriyinceye kadar karıştırılır. Daha sonra hiposülfat, soda ve suyun geri kalanı eklenir. Bir litrede serbest olarak bulunan sodyum siyanür 7 g'dır. Çözelti, çevre sıcaklığında ya da sıcakken kullanılabilir.
Rahatlık ve basitlik acısından soğuk çalışma tercih edilir. Bu şartlar altında azami akım 0.2 A/dm2' dir. Sodyum karbonatın çözeltisinin iletkenliğini artırır. Hiposolfit bakır katmanına parlaklık kazandırırken, akımın verimi % 100'den azdır. Sonuç olarak, katotta gaz oluşumu vardır. Aşırı akım bakır katmanın yanmasına, dolayısı ile az ya da çok koyu bir renge bürünmesini sağlar. Normal akım şartlarında parlaklık meydana gelemiyorsa çözelti bozulmuş demektir. Genelde hiposülfat eksikliğinden kaynaklanan bu durumda, gerekli ilaveler yapılır.
İki çözeltinin özelliklerinde ki farlılıkları şu şekilde özetleyebiliriz.
Asitli, bakır nitratlı çözelti: Dengeli aynı zamanda daha fazla kalınlık, % 100'e yakın randıman ile elde edilir. Demir ve çinko doğrudan kaplanamaz, koku ya da gaz mevcut değildir daha yumuşak katmanlar oluşur.
Siyanürlü çözelti: Nüfuz etme gücü daha fazladır. Daha düşük randımanla Demir, çinko, kalay ve alaşımları kaplanabilir. Herhangi bir kalınlığa erişilemez.
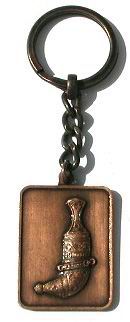
Resim 23: Bakır Kaplama Anahtarlık
2.2.5. Nikel Kaplama
Sembolü Ni, atom ağırlığı 58,71, yoğunluğu 8,9, kaynama noktası 3177 °C Nikel kaplama sarımsı beyaz, yüzey tabaka rezistansı için net yansıyan görünümde, lehimlenebilir özelliktedir tercihen çalışmayan mekanik aksamların imalatında kullanılır. Nikel kaplama genellikle çelik, bakır ve krom altı dekoratif amaçlı olarak uygulanır. Nikel genel olarak paslanmaz çelik başta olmak üzere, korozyona dirençli alaşımların eldesinde kullanılan bir elementtir. Madeni paraların, nikel-kadmiyum pillerin ve zırh kaplamalarının yapımında da yararlanılır. Nikel kaplama, diğer metalleri koruyucu özelliktedir. Korozyona karşı dayanıklı oluşu nedeniyle, elektrolizle kaplama işlemlerinde de tercih edilir (http://www.odevarsivi.com).
Resim 24: Seri Üretim Nikel Kaplama Ünitesi
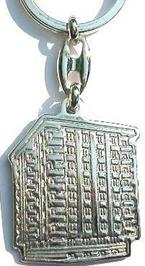
Resim 25: Nikel Kaplama Anahtarlık
2.2.6. Bakır, Nikel ve Alaşımları Üzerine Gümüş Kaplama
Gümüş siyanürlü çözeltiler, sadece daldırma sureti ile bakır ve alaşımlarını kaplama özelliğine sahiptir. Bu kaplama, iyi yapışmadığından bu metotla gerçekleştirilen işlem kaliteli değildir. Bunun önlenmesi için, nesneler daha önce civa siyanürü içeren bir çözeltiye batırılırlar. Bu karışım, aşağıdaki gibi hazırlanabilir
(1 litre için):
Civa biklorür 5 g
Sodyum siyanür 15 g
Yağı alınmış ve yıkanmış nesneler bu solüsyona daldırılır ve tipik parlak beyaz-gri renk elde edilinceye kadar karıştırılırlar. Bol su ile yıkanıp gümüş kaplanır. Özellikle ince olması halinde, sertleştirilmiş pirincin işlenmesi tavsiye edilmez. Kırılganlık oluşturur. Bu durumda pirinç tekrar ısıl işleme tabi tutulmalıdır tavlanmalıdır. Civa karışımı, tahliye de sorun olduğundan ön gümüş kaplaması uygulanır, işlemi müteakip, normal galvaniz işlemine geçilir. Bu arada işlem sadece bakır ve alaşımlarında değil, nikel ve alaşımları ile alpakada da kullanılabilir.
İnce bir gümüş katmanı oluşturulacak şekilde çözelti hazırlanır. Bu katmanın üzerine ikinci kaplama gelecektir. Az Ag ve çok siyanür içeren çözelti şu şekilde oluşturulabilir:
Sodyum siyanür 60 g
Ag nitrat 3g
Arı suyu 1 (Litre)
Azami akım 2 A/dm2; ortam sıcaklığı, demir anot, cam, demir ya da plastik havuz. İşlem yarım dakika kadar sürmelidir. Modern bir karışıma göre: Ag siyanürü 3,5 ila 5 g/l Potasyum siyanür 75 ila 90 g/l; sıcaklık 20 ila 30 °C Akım 1,5 ila 2,5 A/dm2 4 ila 6 V Serbest siyanür miktarı 73 ila 87 g/l; Ag miktarı 2.8 ila 4g/l Bu tür işlemlerde Ag tuzu ve siyanür kullanılmak suretiyle bakım yapılır (VITIELLO,2006,s.380).
2.2.7. Metal ve Değişik Alaşımlarda Gümüş Kaplama
Galvaniz işlemiyle demir, kalay, çinko gibi metaller gümüşle kaplanarak değeri arttılıyor.
2.2.7.1. Demir Malzemeleri İçin
Kaplama için iki kat gereklidir; ilki Ag- Cu özlü çözeltilerde gerçekleştirilir.
Ag siyanür 2g/l
Cu siyanür 11g/l
K siyanür 74g/l
Sıcaklık 20 ila 30 °C; akım 4 ila 6 V, 1,5 iia 2,4 A/dm2 süre 1 2 dakika. Anot demir esaslı malzeme veya paslanmaz çeliktir. Havuz, demir esaslı, ise akımın pozitif ucu ona bağlanır. İlk kat oluşturulduktan sonra (sürüldükten sonra) yıkanır ve ön gümüş kaplaması yapılır sonra ikinci kaplama işlemine geçilir (VITIELLO,2006,s.381).
2.2.7.2. Çinko Alaşımları
Çinko kaplama genel olarak demir veya metallerin çinko ile kaplanmasıdır.
Bu kaplama çinko oksit, sodyum siyanür, hidroksit kimyasalları eriği ile çinko metalin elektroliz yoluyla parçaların üzerine kaplanmasıdır. Siyanür banyosunda bakır kaplanır, ön gümüş atılır ve galvaniz yapılır.
2.2.7.3. Kalay Alaşımları
Çinko gibi işlem yapılır. Alaşımın belli miktarda gümüş ihtiva etmesi halinde doğrudan galvaniz işlemine geçilir.
2.2.7.4. Selektif Kaplama
En başından beri gümüş ustası "hatalı üretimleri nasıl telafi ederim problemi ile karşı karşıyadır. Ya rötuş yapma, ya da tüm işlemi başta-gerçekleştirme gereklidir. Bunun sonucu olarak, rötuş kaplaması ortaya çıkmıştır. Bir Ag çubuğun ucuna çözelti emdirilmiş kumaş sarılır ve negatif uca bağlanmış nesnenin hatalı taşımalarına sürülürdü.
Günümüzde bu işlem sistematik üretim amaçlı kullanılmaktadır. Gerek çözeltiler geliştirilmiş olup, yüksek akım değerlerinde, 2 ila 10 saniye arasında yeterli kalınlıklar oluşturabilmektedir. Katkı maddelerinin kullanılması ile istenilen özellikte katmanlar oluşur. Bu metot değerli metal tasarrufu sağlamak amacı ile ve Ag'nin, sadece bir yüzeye kaplanacağı durumlarda kullanılmak üzere oluşturulmuştur. Eriyebilen Ag anodu, ya da erimeyen platin ya da platin" kaplı titanyum anotlar kullanılır. 45 ila 70 "C arasında kullanılır. Anot yüzey, büyüklüğü, katodunkinin 2 ila 5 kat, olmalıdır. Akım 50 ila 200 A/dm2.Bu metot tüm galvaniz türlerinde uygulanabilir (VITIELLO,2006,s.382).
Serbest siyanür azlığı, aşağıda sıralanan olumsuz etkilerden bir ya da bir kaçına yol açabilir: Parlak ya da süt beyaz olmayan kaplama, sarı ile koyu renk arası tonlar, çıkıntılarda siyahlık, çözeltinin sarılaşması, parmak üzerinde duyarlılık, pürüzlü, kaba yüzeyler, nesneler çözeltide iken volt ibresinin artması, ampermetreninkinin düşmesi, yetersiz kalınlık, kirli ya da siyahlaşmış anot.
Akımın çokluğu bazı sorunlara yol açar bunlar; yapışmayan, tonlu, tozlu katmanlardır. Kaplamanın ayrılması akım fazlalığından, alt katmanın oksitlenmiş olmasından ya da bulunmamasından, yağların temizlenmemesinden kaynaklana bilir.
Yetersiz kalınlığın sebepleri; düşük akım, yetersiz süre, kalitesiz elektrik bağlantılarıdır. Parlak yüzey, portakal kabuğu görünümünde ise, nedeni eksik mekanik işlemlerdir.
2.2.7.5. Siyanürsüz Gümüş Kaplama
Son yıllarda, kirlenmeyi önlemek amacı ile siyanürsüz çözeltilerin arayışına gidilmiştir. Bu anlamda sodyum veya potasyum iyodür siyanürün yerine, sodyum tiosülfat ile eritilmiş Ag klorür ya da sülfat kullanılan çözeltiyle türetilmiştir. Derişik bir seçenek ise Ag iyodürün derişik potasyum iyodür çözeltisinde eritilmesidir. Özel katkı maddeleri sayesinde kaliteli ürünlerin elde edilmesi mümkündür. Bu tür çözeltiler pek yaygın değildir (VITIELLO,2006,s.383).
2.2.7.6. Çatal Kaşıkların Gümüş Kaplanması
En kaliteli üretim şekline göre, yüksek oranda nikel içeren alaşım haddelenir ve baskı ile şekillendirilir. Bu şekilde çok dayanıklı ürünler elde edilir Günümüzde döküm işlemeleri kullanıldığından, mekanik özelliklerin kalite; düşüktür. Yüzey tam anlamı ile düz olmayıp, elastikiyeti azdır. Büküldüğünde kırılmakta, kırılan yüzey pürüzlü olmaktadır. Bu durum, özellikle çatal uçlarında görülür. Temizliğinde, aşındırıcı maddeler kullanılmamalıdır. Kullanıldıkça parlaklık artmaktadır.
Elektrotlarda Ag'nin kalitesi: Anot saf Ag olmalıdır. Çözeltinin durumuna dağılımına ve akımın yoğunluğuna göre değişik yüzey renkleri gerçekleşebilir. Bazı şartlar altında, kesin beyaz bir yüzey oluşur. Diğerlerinde kristal ya: meydana gelir, aşınma genel ve düzensizdir. Renk buna bağlı olabilir. İyi bir üretici, anodun içerdiği yabancı maddelerden dolayı, çözülmeyen siyah tuz e kaplanmayacağına dair garanti vermelidir. Sıkça, olarak anoda diğer sebeplerden kaynaklanan kusurlar da yüklenir. Örneğin yüksek akım, düşük pH, serbest siyanür fazlalığı, anot ve katot arası bozuk dağılım, yabancı maddeler. Her halükarda, anotların hareket ettirilip, filtre düzeneğinin bulunması tavsiye edilir.
Şartlar müsait olduğunda katotta oluşan katman süt beyazı olup kolaycı parlak kadife görünümündedir. Akımın fazlalığı, düzensiz kaplamalara ye açar.
Gümüş kaplama parlaklığın dışında denge, hava ile temas halinde dayanıklılık gibi özellikleri sağlayan çözeltiler kullanılmaktadır. Anot yüzeyi, katottakinden en az iki kat büyük olmalı hiç bir surette kaplanacak nesnelerin altına inmemelidir (VITIELLO,2006,s.381–382).
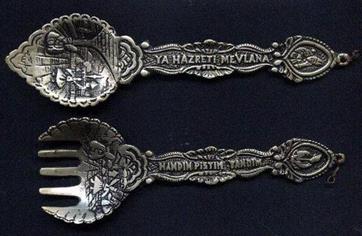
Resim 26: Gümüş Kaplama Çatal Kaşık
2.2.8. Galvano Plastik
Kalınlık işlemlerinde aşağıda belirtilen çözelti kullanılabilir.
1 litre arı suda;
Ag siyanürü (50 g/I'ye karşılık gelen 62,5 g/l
Sodyumsuz potasyum siyanür 150 g/l
Serbest potasyum siyanür 89 g/l; 0.3 A/dm2; sıcaklık 15 ila 20 "C'dir Meta.» vernikle kaplanıp fırında pişirmek sureti ile ince bir Ag metalik katmanı ile kaplanır. İnce bir Ag katmanına sahip olan porselen ve camların kaplanmasında kullanılır.
Bu solüsyon tüm galvano plastik işlemelerinde kullanılabilmektedir. Ortam sıcaklığında işlem yapıldığından ısıya dayanıklı olmayan kalıplarda kullanılabilir. Çözeltinin sürekli olarak karıştırılıp filtre edilmesi tavsiye edilir (VITIELLO,2006,s.380).
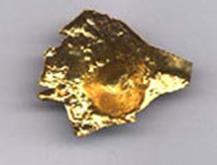
Resim 27: Galvano Plastik
2.2.9. Nikelaj
Altın alaşımı olmayan metallerde, altın kaplamaya ya da değerli olmayan taşımlarda ya da gümüş alaşımlarda yapılacak rodyum kaplamaya zemin olarak kullanılabilir. Gümüşün hava ile teması sonucunda bozulmasını engellemek amacı ile başvurulan metotlardan biri rodyum kaplamadır. Yeterli kalınlıktaki bir katman son derece pahalı olacağından zemin olarak nikelaj işlemi yapılır. Bazı durumlarda parlak nikelajda yeterli olabilmektedir.
İki ayrı çözelti türü verilmiştir. Her ikisi de çevre sıcaklığında kullanılır. Nikelaj için soğuk ortamda ve hızlı şekilde gerçekleştirilen çözeltileri mevcuttur, ancak ısıtma, filtre ve karıştırma üniteleri içeren karmaşık tesisler gerekmektedir. Asiditenin korunması için, kontrol kâğıtları kullanılır ve "sülfürik asit" eklenip eklenmeyeceği anlaşılır. Genelde her 10 litreye 2 ila 3 gram eklenir (VITIELLO,2006,s.377).
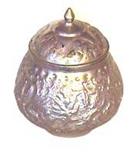
Resim 28: Nikelaj Kaplamalı Şekerlik
2.2.10. Rodyum Kaplama
Rodyum beyaz parlak bir metal olup, yansıtma gücü Ag'ninkinin % 80'i olup, ultraviyole ışınlarında Ag'ninkinden üstündür. Rodyumun tersine Ag'nin yüzeyi Ag sülfürü oluştuğundan bulanıklasın Rodyum ise kesinlikle bozulmamaktadır. Bu metal, yansıtıcı sanayinde de, başarılı şekilde kullanılmakta olup erime sıcaklığı 1966 "C'dır.
Rodyum banyoları sülfürik ve fosforik asit içerirler. Her ikisiyle de son derece iyi sonuçlar elde edilmektedir. Genelde litre başına metal içeriği 2 ila 2,5 g. arasındadır (VITIELLO,2006,s.389).
Rahatlık açısından derişik rodyum tuzu, fosfat ya da sülfatından yola çıkılmakta, su ile karıştırılıp asit eklenmektedir
Kaplama gücü çok yüksektir bu açıdan altın ve gümüş kaplamada tercih edilir. Birkaç saniyede beyaz parlak bir katman ortaya çıkarabilmektedir.
Hem sıcaklık hem akım yönünde geniş bir spektruma sahiptir. Nitekim çevre sıcaklığı ile 60 °C, 1 ila 11 A/dm2 arası çalışabilmektedir. Anot olarak platin teline kaynak edilmiş 1000 milyemlik platin levha kullanılır. Platin, çözülmediğinden sürekli kullanılabilir. Platin kaplı titanyum veya tantalyum kullanılabilir. Cam kaplar uygun olmakta, işlemin sıcak yapılması halinde kimyasal işlemleri için özel camlar tercih edilmektedir (VITIELLO,2006,s.389).
Doğrudan Ag'nin kaplanması tavsiye edilmemektedir. Rodyum katmanı o kadar incedir ki Ag'nin bozulmasını engelleyemez.
Ayrıca, doğrudan rodyum kaplama işlemi, başarılı olmayabilir. Bu ama g ile Rodyumun arasına parlak nikelaj kaplama işlemi uygulanır.
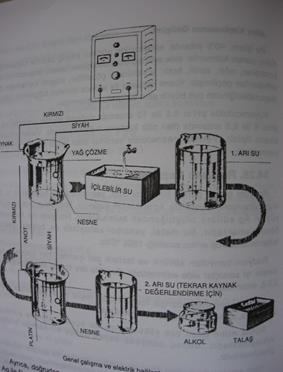
Resim 29: Genel Çalışma Ve Elektrik Bağlantı Şeması
Çözeltiler;
Derişik rodyum çözeltisi (ya da gerektiği kadar) 2,5 g
Saf, derişik sülfürik asit 20 g
Arı su 1 litre
Ortam sıcaklığı; 2,5 g 5V
Derişik rodyum çözeltisi (ya da gerektiği kadar) 2 g
% 85 milyemlik fosforik asit 15 ila 35 g
Arı su 1 litre
Derişik sodyum çözeltisi 2 g.
Saf, derişik sülfürik asit 35 g.
Arı su 1 litre
Sıcaklık 45 ila 50 °C; 2,5 ila 5 V
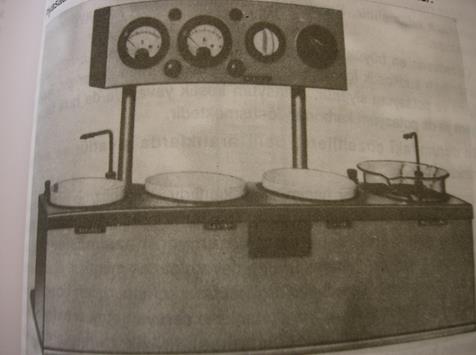
Resim 30: Galvaniz Üretim Tesisleri
Çözeltilerde rodyum, yeni derişik sıvı ile takviye edilmekte ya da çözelti azami şekilde kullanılıp ayrı yere alınmaktadır. Rodyum kaplama da akım randımanı (verimi) düşük olup, azami % 35 ila 40'tır. Bu dutum geniş hidrojen üretimini, bu gazın ortaya çıkması da rodyumun sertliğini açıklamaktadır.
Galvaniz işleminde kalınlık azami 0,1 mikrondur. Kaplama işleminden sonra nesneler arı suyla yıkanır ve alkole batırılır (VITIELLO,2006,s.389–391).
2.2.11. Mücevherlerin Kaplanması
Kuyumculukta kullanılan değerli taşlardan bir kısım tüm kimyasallara karşı dayanıklı iken, bazıları alkali çözeltilere dayanmakta asitlere duyarlı olmakta, bazıları ise asitlere dayanırken alkalilere duyarlı olmaktadır. Sıvılar, sıcak olduğunda dayanıklılık azalmakta, sıcaklık değişimleri tehlikeli olabilmektedir.
Mücevher, taşları ile bir bütün olduğunda, galvaniz işleminin nesneyi tamamıyla daldırılıp mı, yoksa sadece metalik kısmı daldırılarak mı yapılması gerektiği çok önemlidir. Çünkü dikkat edilmese kapla işleminden sonuç alınamaz.
Galvaniz işleminden etkilenmeyen taşlar: elmas, korindon, safir, su safiri, mavi safir, yakutlar ve kuartz. Bu taşlar, hiç bir risk olmadan, çözeltilere batırılabilir. İnciler, mercanlar, pistasit ve diğer taşlar galvaniz çözeltilerine dayanmamaktadır. Aslı, silisyum hidrat olan, opal taşı altın ve gümüş kaplama banyolarında erimektedir.
Galvaniz işleminde uyulması gereken kurallar vardır örneğin taşlı bir nesnenin kaplama işleminde mücevher tamamen işleme tabi tutulacaksa kullanılan taşlar dayanıklı taşlar sınıfından olmalı.
Günümüzde nesneyi etkilemeden birçok metali eritebilmek mümkündür. Kuyumcu, bazen bakır, nikel, kurşun, kalay artıklarını temizleme ihtiyacı duyar.
Çözelti oluşturma kapasiteleri düşük olduğundan, değerli metal tortularının temizlenmesi pek kolay olmamaktadır. Temizleme makinesi her zaman kullanılabilmekte ancak bazen nesnenin, parçalarına ayrılmasını gerektirdiğinden uzun ve sıkıcı bir işlem olabilmektedir. Rodyum kaplamada en iyi metottur.
Rodyumun porozitesinden dolayı, uygulanan kimyasal yöntemler, oluşturulan katmanı parçalayıp ayırmaktadır. Nikel alt katmanının bulunması da yeterli değildir, çünkü nesne parlaklık ve düzgünlüğünü kaybetmektedir. Kimyasal ve galvaniz metotlar kullanıldığında nesne, arada bir çıkartılarak, işlemin gidişatı kontrol edilmekte, aşırı kimyasal etkiden kaçınılmaktadır. Bazı metallerde temizlik işleminin bittiği, ani voltaj ya da amper düşüşünden anlaşılabilir (VITIELLO,2006,s.395).
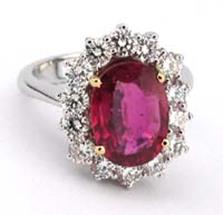
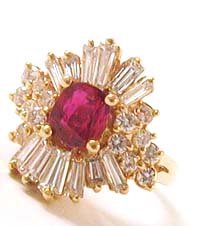
Resim 31: Yakut Yüzükler
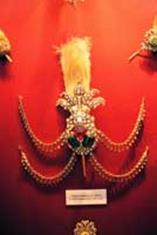
Resim 32: Sorguç
2.2.12. Tombaklama
Bakır ve bakır alaşımlarının "altın-cıva" amalgamı yardımıyla yaldızlanması işlemine "tombaklama", bu şekilde altın kaplama yapılmış parçalara ise "tombak" denir. Tombağın batı dillerindeki anlamı bakır-çinko alaşımı olan yapay bir metaldir. Ne yazık ki bizim sözlük ve ansiklopedilerimize batı dillerindeki bu anlamı "tercüme" edilmiş, dilimizdeki gerçek anlamı belirtilememiştir.
Tombaklama, altın görünümü vermek amacıyla, birçok kaba ve eşyaya yaygın olarak uygulanmıştır. Altının hemen hemen her çağda az bulunan ve çok değerli bir metal oluşu sebebiyle birçok eşya altından yapılamamış, ancak çağlar boyu insanların vazgeçemediği altın tutkusu, kullandıkları eşyaya hiç olmazsa altın görünümü verme arzusunu doğurmuş ve tombaklama yöntemi böylece ortaya çıkmıştır.
Bakır ve bakır alaşımların altın kaplanması (altın yaldızlama) için mekanik, kimyasal ve elektrokimyasal olmak üzere üç ayrı yöntem vardır. Mekanik yöntemde, kaplanacak parça yüksek sıcaklıklara kadar ısıtılır ve hazırlanmış olan altın varak parçanın yüzeyine bastırılarak kaplanır. Kimyasal yöntemde ise iki ayrı yol vardır. Birincisinde özel olarak hazırlanan altın çözeltisine daldırılan parça, başka bir işleme gerek kalmaksızın bir altın tabakası ile kaplanmış olur. İkincisinde ise önce altın amalgamı parça üzerine sürülür ve ardından parça ısıtılarak yüzeydeki cıva uçurulur. Böylece oldukça kalın bir altın tabakası ile kaplama yapılmış olur. Altın, tıpkı kalaylamada olduğu gibi parçaya nüfuz ettiği için son derece dayanıklı bir kaplamadır. İşte bu şekilde yapılan altın kaplama işine "tombaklama" kaplanan parçaya ise "tombak" denir.
Elektrokimyasal yöntem 19. yüzyılın ikinci yarısında geniş kullanım alanı bulmuş bir yöntem olup "elektroliz yöntemi" olarak da adlandırılır. Altın içeren sulu çözeltiye kaplanmak istenen parçanın daldırılıp elektrik akımı yardımıyla altın kaplanmasıdır. Tombaklama beş aşamada gerçekleştirilir.
1. Altın amalgamın hazırlanması.
2. Altın kaplanacak metalin yüzeyinin temizlenmesi.
3. Altın kaplanacak metalin yüzeyine altın amalgamın sürülmesi.
4. Civanın metal yüzeyinden uzaklaştırılması.
5. Kaplamanın istenen renge kavuşturulması (http://www.antikalar.com/v2/konu/konu0107.asp).
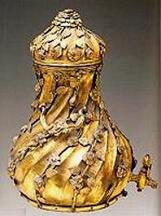
Resim 33:Tombak Tekniği
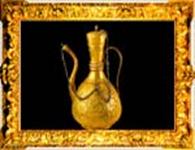
Resim 34: Tombak Tekniği
III. BÖLÜM
GALVANİZ YAPIM ORTAMI VE GALVANİZ İŞLEMİ
3.1. GALVANİZ YAPIM ORTAMI
Galvanizin (kaplamanın) yapılabilmesi için yapım ortamlarına ihtiyaç vardır. Bunlar aşağıda ayrıntılı bir şekilde açıklanmıştır.
3.1.1. Galvaniz Konusunda Temel Bilgiler
Galvaniz konusunda ki temel kavramları kısaca tanımak gerekirse;
3.1.1.1. Yoğunluk Özgül Ağırlık
Bir cismin 1 ml. sinde bulunan çözelti kütlesidir (d) ile gösterilir. Çökelti kütlesi (gr.), çökelti hacmi (ml.) dir. Kısaca d = gr /ml dir.
3.1.1.2. Yüzde
Bir çözeltinin 100 gramında bulunan çözünmüş maddenin kütlesidir.
3.1.1.3. Konsantrasyon
Çözeltinin 100 ml. sinde bulunan çözünmüş maddenin kütlesidir. Konsantrasyonu 20 olan bir çözelti demek; 20 gram madde 100 ml. çözücüde çözünmüş demektir.
3.1.1.4. Elektrolit
Elektroliz kabında (+) pozitif kutup ANOT, (–) negatif kutup KATOT adını alır. Elektrik akımını geçiren maddelere İLETKEN, elektrik akımını geçirmeyen maddelere YALITKAN adı verilir. Anoda giden (–) negatif yüklü iyonlara ANYON, katoda giden (+) pozitif yüklü iyonlara da KATYON adı verilir.
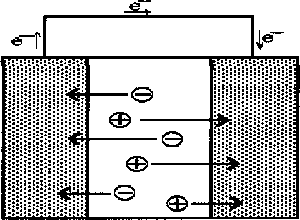
|
Polimer
|
Elektrolit
|
Polimer
|
Resim 35: Elektrolit
3.1.1.5. Elektroliz
İyonlara ayrılabilen bir cismin sulu çözeltisinde, su dipollerinden ibaret bir cins bulutla çevrili, yani hidratize olmuş (+) ve (–) yüklü iyonlar vardır. Bir bakır klorür (CuCl2) çözeltisinde sudaki (H+) ve (OH-) iyonlarının yanında (Cu+) ve (Cl-) iyonları bulunur.
Bu çözeltiye iki platin levha sokup bir doğru akım kaynağının iki farklı kutbuna bağlayıp akım geçirirsek: (+) yüklü (Cu++) iyonları negatif elektroda KATOD'a gider. (-) yüklü (Cl-) iyonları ise pozitif yüklü elektroda ANOD'a gider. Cu++ iyonları katotta elektrik yüklerini bırakırlar. Her bakır iyonu elektrottan iki elektron alır, böylece Cl- iyonları elektrikçe nötral olan klor gazı haline geçerler. Kaplama işlemi yapılmış olur (Berk, V “ Yüzey İşlemler Teknolojileri I ’’ Yüksek Lisans Tezi, 121s, (2004).
Elektrolitik kaplamanın "Galvano teknik" yani metal kaplamacılığının temelini işte bu elektroliz olayı oluşturur.
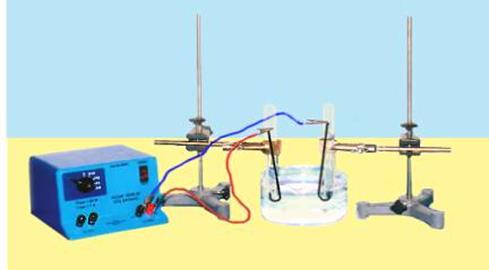
Resim 36: Elektroliz Düzeneği
3.1.1.6. OHM Kanunu
Ohm; içinden 1 Amper’ lik akım geçtiğinde iki nokta arasında 1 Volt’ luk potansiyel farkı gösteren bir iletkenin bu iki nokta arasındaki direncidir.
3.1.1.7. Direnç
Bir iletkenin direnci onun boyu (l) ile doğru orantılı, kesiti (s) ile ters orantılıdır. Direnç (R) ile gösterilir.
3.1.1.8. Volt
1 Ohm'luk bir dirençten 1 Amper geçiren kuvvettir.
3.1.1.9. Amper
Akım şiddeti birimidir. Bir iletkenden zaman biriminde geçen elektrik miktarıdır. Yani 1 Amper bir iletkenden 1 Saniyede 1 Coulomb geçirilmesiyle elde edilir.
3.1.1.10. Coulomb
Bir gümüş nitrat çözeltisinden 1,118 mg. gümüş açığa çıkaran elektrik miktarı 1 coulomb (kulon)’ dur.
3.1.1.11. Faraday Kanunu
Herhangi bir iyonun 1 ekvivalent gramının nötr element haline geçebilmesi için daima aynı miktarda yani 96.490 coulomba ihtiyacı vardır. Yani elektrolizde elektrolitin 1 ekvivalent gramını açığa çıkaran elektrik miktarıdır. Bu da 96.490 coulomb'dur ve elektronun yükü ile Avagadro sayısının çarpımına eşittir.
Faraday (F) = 96.490 coulomb veya
(F) = 96.490 Amper-saniye veya
(F) = 26,801 Amper-saat
1 coulomb = 1 Amper-saniye
1 c = 1 As
1 saat = 3.600 saniye
1 Ekvivalent e de er = 96.490 /3.600 = 26,8 Ah
Galvanoteknikte amper-saat geçerlidir.
1 Amper-saatte ayrılan metal miktarı (e) elektrokimyasal eşdeğer olarak bilinir (Berk, V “ Yüzey İşlemler Teknolojileri I ’’ Yüksek Lisans Tezi, 121s, (2004).
3.1.1.12. Akım Yoğunluğu
Galvano teknikte akım şiddetinin yerine, elektrotların birim yüzeyine isabet eden akım şiddeti alınır. Buna akım yoğunluğu denir. Birim yüzey dm2 dir.
3.1.2. Galvanizin Uygulama Alanları
Rodyum kaplama için kullanılan malzeme beyaz altın-paladyum-platin-gümüş-beyaz ya da gri alaşımlardır. Kaplamanın amacı alaşıma bozulmayan parlak beyaz renk vermek; kaynaklardaki değişik rengi örtmek; yüzey sertliğini artırmak; yansıtma gücünü arttırmak. Gümüş kaplama için kullanılan malzeme gümüş alaşımları ve altın alaşımları kaplamanın amacı 1000’lik gümüş rengini sağlamak, antik gümüş oluşumunu desteklemek. Altın kaplama için kullanılan malzemeler altın alaşımları ve gümüş alaşımları kaplamanın amacı kaynakların değişik rengini örtmek, 1000 milyemlik altın rengini sağlamak, artık renklendirme işleminde kullanılmayan renkleri tutturmak. Parlak için kullanılan malzemeler ise gümüş alaşımları, kalay, çinko, alüminyum alaşımları amaç ise gümüşün kararmasını önlemek; altın ve rodyum kaplamaya alt zemin oluşturmak, diğer galvaniz işlemlerine alt zemin oluşturmak (VITIELLO,2006,s.364).
3.1.3. Galvaniz İçin Gerekli Malzemeler
Doğru akıma dönüştürülecek, sanayi amaçlı ya da aydınlamada kullanılan elektrik enerjisi. Dalgalı akımı doğru akıma çevirebilen güç kaynağı. Isıtma amacı ile gaz ya da elektrik akımı (Gaz daha hassas olarak ayarlanabilir). Yıkama suyu (Son yıkamada arı suyu da deiyonize eden su kullanılmalıdır). Değişik sıvıları ihtiva edecek kaplar (Kullanılacak malzeme, çözeltilere göre farklılık göstermektedir). İşlenecek nesneleri bağlayacak metalik teller (Oksitlenmiş bakır kullanılabilir). Akımı geçirecek ve çözeltiye batırılacak metalik levhalar. İki adet kutup gereklidir; bir tanesi nesne olup, diğeri levhadır. Kurutulacak nesnelerin batırılacağı alkol. Gümüş kaplama tesislerinde ve seri üretimlerde alkol yerine hava ya da sıcak talaş kullanılabilir. Kurutma için sıcak odun talaşı (VITIELLO,2006,s.365).
3.1.4. Galvaniz İşleminde Akımın Ayarlanması
Herhangi bir galvaniz banyosunda, rasgele volta ya da amper de çalışma yapılamaz. Belli gerilim (volt) ve akım yoğunluğu (amper) limitleri dahilinde çalışmalıdır. Bu amaca ulaşabilmek amacı ile akımın ayarlanabilmesi şarttır.
Doğrultucularda - ikinci devredeki kalın spiraller boyunca ilerleyen akımın şiddeti, sıfırla azami değer arasında değişebilir. Bu kontrol aracı ile bu aya-yapılabilmektedir. Üretim yüklü olduğunda, zaman kazanmak amacı ile iki ayrı redresörün kullanılması yerinde olacaktır, ilk banyo hazırlık amacı x yağların temizlenmesinde kullanılmaktadır. Redresör tek ise, banyonun biri dolu iken, ikincisinin boş bulunması gerekir. Etkili ölçüm aygıtları: Voltmetre ve ampermetre -Elektrik akımından bahsedilirken volt ve amper denilen iki ana özellik ayırt edilmektedir (VITIELLO,2006,s.366).
Volt ile akımı dolaşmaya iten güç ifade edilirken, amper ile saniyede geça~ akım miktarı (Yoğunluğu) ifade edilmektedir.
3.1.4.1. Voltmetre Ampermetre
Galvaniz işleminde, azami 10 ila 15 Volt'a çıkabilen cihazlarda bu ölçeğin bulunması yeterlidir. Akım yoğunluğu ise işlenecek nesnenin yüzey alanına ve uygulanacak işleme göre daha geniş yelpazeye sahip olmaktadır. Yağ çözme işlemi azami düzeyde yoğunluk gerektirir (10 A). Sonuç olarak 10 A'lik ampermetreler uygun olabilmektedir. Bu yoğunluktaki bir ampermetre, bazı durumlarda, sağlıklı okumalar vermeyeceğinden, daha düşük ölçekli ampermetreler kullanılmalıdır.
Bu ölçme aygıtlarının iki çeşidi vardır; hareketli bobin ya da hareketli ibreli aygıtlar ölçeğin tasarımından ayırt edilebilmektedir. Hareketli bobin türlerinde, geçen akımla iğnenin hareketi arasında sabit bir oran vardır, Sonuç olarak, kadrandaki aralıklar aynıdır. Bu aygıtlar en hassastır. Kutupların yeri değiştirildiğinde, iğne yön değiştirmektedir. Bu özelliği sayesinde, bir akım jeneratörünün kutuplarının tayininde kullanılabilmektedir (VITIELLO,2006,s.367).
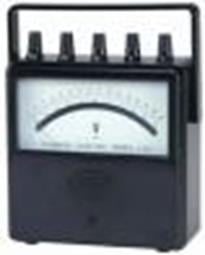
Resim 37: Voltmetre-Ampermetre
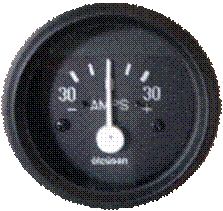
Resim 38: Voltmetre Resim 39: Ampermetre
3.1.5. Artı Kutup ve Eksi Kutuplar
Doğrultucularda kabloların bağlantı yerleri kırmızı ve siyah, kırmızı ve yeşil gibi renkler ya da (+) ve (-) gibi işaretlerle ayırt edilmiştir. Bu kutuplardan çıkan kablolardan biri, metal levhaya, diğeri ise kaplanacak nesneye bağlanmaktadır. Bu bağlantıların yeri değiştirilemez, çünkü akım geçişi başladığında kutuplardan bir tanesi azalmakta, diğeri ağırlık kazanmaktadır, ilk kutup pozitif (+) olarak adlandırılır ve kırmızıya bağlanmalıdır. Diğer kutup ise negatif olup, (-) işaretli, ya yeşil, ya da siyah çıkışa bağlanmalıdır.
Bazı galvaniz banyolarında (parlatma ya da alüminyumun oksitlenmesinde kullanılan) nesne artı kutup görevini görmekte, yani "anot" olmaktadır. Genelde, nesne; yağ çözümünde, altın, gümüş ve rodyum kaplamalarında "katot" da denilen negatif kutup görevi görür.
Banyo
|
Takımın Bağlandığı Kutup
|
Levhanın Bağlandığı Kutup
|
Levha Türü Metal Levha Malzemesi
|
Yağ Altın
|
Negatif Negatif
|
Pozitif Pozitif
|
Yağ çözme, Altın kaplama,
|
Gümüş Rodyum
|
Negatif Negatif
|
Pozitif Pozitif
|
Gümüş kaplama Rodyum kaplama
|
Nikelaj
|
Negatif
|
Pozitif
|
|
Altın
|
Pozitif
|
Negatif
|
Altın parlatma
|
Tablo 2: Kuyumculara Uygun Veriler
3.1.6. Akım Yoğunluğu Doğrultusunun Gücünün Seçimi
Akım yoğunluğu sabit tutularak aynı banyoya sırası ile batırılan nesnelerden geniş yüzeyi olan nesnelerin daha az akım toplayacağı açıktır. Akım yoğunluğunun, yüzey alanına bölünmesiyle elde edilen değer, birçok amaçla kullanılır.
İşlenecek en büyük nesne bilindiğinde, gerekli olan maksimum akım ve dolayısı ile redresörün gücü hesaplanabilir. Örnek olarak; en büyük nesnenin 10 dm2'lik tepsi olduğunu varsayarsak en az 50 A'lik bir redresör gereklidir. Çünkü her dm2 için 5 A gereklidir. Yağ çözmek için ise genelde 0,3 A/dm2 ile çalışıldığından için en az 3 A'lık bir redresör gerekli olacaktır. Hızlı biçimde, gümüş kaplamasında 50 A'lık redresörün kullanılması uygundur (VITIELLO,2006,s.369).
Her galvaniz banyosunun akımın belli alt ve üst sınırları mevcuttur. Ancak bu sınırlar dahilinde çalışıldığı takdirde başarılı sonuç alınabilmektedir. Akım çok düşükse, nesne ya kaplanmamakta ya da eksik kaplanmaktadır. Akım aşırı yüksek olduğunda ise kaplama çirkin ya da "yanmış" gibi görünmektedir. Galvaniz tecrübesi olmayanlar bile deneme yanılma yolu ile en uygun akımı tespit edebilmektedir.
Ayrıca saniye, dakika ya da saat başına metal kalınlığındaki artış hızının hesaplanmasında kullanılabilir.
3.1.7. Galvaniz Tortusunun Özellik ve Kusurları
Kaplama ve nüfuz etme gücü burada galvaniz katmanı nesnenin tümünün üzerine ya da en azından rötuşu ilgilendiren bölgelere yayılmalıdır. Bu yayılma, hiç bir zaman homojen olamamaktadır. Banyonun kaplama gücü ne kadar kaliteli ise yayılma o kadar dengeli olacaktır. Elektrik bilgisine dayanarak elektrik yüklerinin çıkıntılı ve özellikle sivri uçlarda biriktiği söylenebilir. Girintilerde, bu yükler azalmakta hatta bazen yok olabilmektedir. Bir kaşığı ele alırsak, çukur kısım daha az galvaniz kaplamasına maruz kalacaktır. Bir banyonun çukur kısımlarda bile kaplama teşkil edebilme özelliğine nüfuz etme gücü denir. Bir rodyum banyosu, tükenmeye başladığında, çukur kısımlara az ya da hiç kaplama yapmamaktadır. Bu durumda nüfuz etme gücünün azaldığı söylenebilir.
Bir galvaniz katmanının kalitesine karar vermek amacı ile hem çıkıntıların hem girintilerin incelenmesi şarttır. Eğer uçlar uygun değilse, iki nedeni olabilir. Ya akım çok yüksektir, ya banyo tükenmiştir ya da özelliği bozulmuştur. İlk neden geçerli ise, buna "yanma" denir. Daha düşük akım şiddetinde işlem tekrarlandığında katman düzelecektir. Eğer banyo bozulmuş ya da tükenmiş ise çözüm yoktur. Katman her tarafta mükemmel, girintilerde eksik ve kalitesiz ise; ya akım düşüktür ya da banyo bozuktur (VITIELLO,2006,s.370).
Yapışma özelliği bir galvaniz katmanının en önemli özelliği temel metale yapışma özelliğidir. Galvaniz yolu ile o kadar güçlü yapışma elde edilebilir ki, eğme, kesme gibi işlemler bile dökülmeye yol açmamaktadır; eğeleme bile katman ile temel metalin arasındaki bağı kesin bir hat boyunca ayıramamaktadır. Yapışmanın kontrolü, ince bir levhanın bükülmesi ile yapılır. Kabarcık ya da talaş meydana gelirse yapışma iyi gerçekleşmemiştir. Bazen bu kusur; nesnenin kaynar suya batırılması ile ortaya çıkar. Diğer bir metot ise alpaka ya da demir telli fırçalarla işleme yapmaktır. Eğer yapışma yetersiz ve bu kusur ne banyo ne de akıma bağlanabiliyorsa, yağların yeterince çözülmediği ortaya çıkar. Metal iletkenlerin kesiti, batırılan nesnelere ulaşacak olan akım yoğunluğuna uygun olmalıdır. Genelde bu iletkenler bakırdan olup, havuzların dışında Al kullanılabilir. Bu durumda 1 mm2'lik kesitten, azami 1 A geçirilmelidir. Bakır da ise, akım 1.5 A'ya kadar yükselebilir (VITIELLO,2006,s.370).
Sertlik galvaniz yolu ile kaplanan bir metalin sertliği aynı metalin, eritme yolu ile elde edileninden değişik olabilir. Bu durumda, metalin sertleştiği söylenebilir.
Kuyumculukta rastlanılan bir örneği, rodyum kaplamadır. Aynı yolla sert altın, sert krom, sert nikel, sert bakır elde edilir. Lekelenme kusuru bulanık sıvıya ya da eksik çözeltiye bağlıdır.
3.1.8. Galvaniz Katmanının Ağırlığı ve Kalınlığı
Kaplama süresi ve akımın şiddetinden, nesnenin üzerine toplanan metalin ağırlığı hesaplanabilir. Kalınlık hesaplanmak istenirse nesnenin yüzey alanı da bilinmelidir. Ağırlık ve yüzey alanının bilinmesi halinde kalınlık hesaplanabilmektedir. Aşağıdaki tablonun incelenmesiyle, 1 dm2 üzerine 1 mikronluk kalınlığın elde edilmesi, için hacim kütlesi kadar kütleye ihtiyaç olduğu görülmektedir. Ag'nin hacim kütlesi 10,49 olup, 1 dm2'nin üzerine 1 mikronluk kalınlık için 10,49 cg yani 0,1049 g. gereklidir. 1 dm2 üzerine 1 mikronluk kalınlığın elde edilmesi için gereken metal ağırlığı (VITIELLO,2006,s.371).
Metal
|
Gram
|
Santigram
|
Gümüş
|
0.1049
|
10.49
|
Nikel
|
0.0890
|
8.90
|
Altın
|
0.1932
|
19.32
|
Platin
|
0.2145
|
21.45
|
Bakır
|
0.0896
|
8.96
|
Rodyum
|
0.1244
|
12.44
|
Tablo 3:Ağırlık ve Yüzey Alanı
Metal
|
İşlemin Adı
|
dm2'ye düşen gram
|
Kalınlık (Mikron)
|
|
Hafif gümüş kaplama
|
0.30 * 0.40
|
2.8 ile 3.8
|
Gümüş
|
Ağır gümüş kaplama
|
1.5
|
14.3
|
|
Teknik amaçla kullanılan ağır gümüş kaplama
|
5.125
|
50ii
|
Altın
|
Renklendirme
|
0.019*0.050
|
0.10*0.36
|
Bakır
|
Bakır kaplama
|
0.8* 1
|
8.97+ 11.2
|
Rodyum
|
Rodyum kaplama
|
azami0.0124
|
azami 0.1
|
Tablo 4: Kaplamada Kullanılan Metal Kalınlıkları
(Kaplamanın altın ayarı ile kalınlığı mikron cinsinden ifade edilir)
Son teknolojiler sayesinde tahribatsız yöntemlerle bir metalin üzerine kaplanmış olan diğer bir metalin kalınlığını ölçebilen cihazlar mevcuttur. Bu amaçla elektron ışınlarının, diğer bir ismi ile beta parçacıklarının elektromanyetik özellikleri kullanılmaktadır (VITIELLO,2006,s.371).
Metal
|
Nesneye yapışan, yani
|
|
çözeltiden eksilen ağırlık.
|
Gümüş
|
4.025 Gram
|
Nikel
|
1.095 Gram
|
Altın
|
7.356 Gram
|
Bakır
|
Siyanürlü banyodan 2.371 Gram
|
Bakır
|
Asitli banyodan 1.186 Gram
|
Rodyum
|
1.280 Gram
|
Tablo 5: 1 Saat Boyunca 1 Amperlik Akım Geçişi Sırasında Kaplanan Metal Ağırlığı.
3.1.9. Filtreleme
Filtreleme çok önemlidir en basit filtre şekli şudur; banyo bir kaç gün boyunca dinlendirilerek, yabancı maddelerin dibine oturması beklenir. Kauçuk bir hortumla berrak kısım alınır ve bulanık kısım atılır. Bu metot özellikle "yağ çözme" banyolarında kullanılır.
Asıl metallerin banyolarında veya tüm banyolarda en iyi filtreleme metodu, kâğıt filtre ile yapılanıdır. Tamamen berrak sıvı elde edilmesini sağlamakta, sıvının tümünün kullanılmasına imkân vermektedir. Düz veya katlı filtre kullanılabilir. Çok dağınık bir malzemenin bulunması halinde, sonuç düşük hızla filtre yaparak elde edilir. Eğer sıvılar berrak olarak muhafaza edilmezse, galvanizden optimum sonuçlar elde edilemez ve verimli olmaz (VITIELLO,2006,s.372).
3.2. GALVANİZ İŞLEMİ
Galvaniz işlemi bir metalin daha değerli bir başka metal ile kaplanması işlemidir. Kaplama işlemi kaplanacak olan nesnenin temizlenmesi ile başlar daha sonra sırasıyla banyoda kaplama ve cilalama işlemleri ile son bulur.
3.2.1. Galvaniz İşlemi
Galvaniz işlemi sırasında mutlaka yapılması gerekilen işlemlere kısaca bakılacak olursa;
3.2.1.1. Kaplanacak Parçaların Temizlenmesi
Yapışık ve dayanıklı bir tabakanın elde edilmesinde en başta gelen faktör yüzeyin temizliğidir. Herşeyden önce metalin kimyasal olarak meydana çıkması lazımdır. Öteki faktörler ne kadar iyi tayin edilip tatbik edilirse edilsin, kaplanacak yüzey fevkalade temiz değilse, diğer bütün işler boştur. Bir temizleme işlemi esas olarak sıra ile şu aşamaları kapsar mekanik yolla parçanın temizlenmesi; yağ çıkarma; oksid tabakasının giderilmesi.
Mekanik yolla maddenin temizlenmesi (polisaj) bu işlemde çelik telden yapılmış fırçalarla zımpara taşları ve törpüler kullanılır ve metalin yüzeyi düzeltilip yabancı maddeler kaldırılır.
Zımpara maddesi olarak elektrik fırınında çok saf alüminin eritilmesinden elde edilen korindon ; karborandum SiC; bor karbür B4C; vanadium nitrür VN; pişirilmiş dolomi; demir oksid kullanılır. Bu çeşitli cisimler elekten geçirilmiş tane büyüklükleriyle fark ederler. Bu zımpara maddeleri muhtelif bağlama maddeleriyle ekseriya disk halinde imal edilirler. En fazla kullanılan seramik bağlamada aglomerasyon, az miktarda feldspat, kuvars, kalker v. b. ihtiva eden eriyebilen camların 1300 - 1500°C' da ısıtılması ile elde edilir. Seramik bağlama hemen tamamiyle korindon ve karborandum için kullanılır ki sıcakta müteessir olmazlar. Sentetik reçine, gom laque, çimento da bağlama maddesi olarak kullanılır. Parlak polisaj için deri yahut kumaş ve hatta kağıtla kaplı diskler kullanılır. Son yıllarda parlak polisajın kalitesini arttırmak için kumaş disklerden evvel polüretan bağlantılı aşındırıcı disklerin kullanımı yaygınlaşmıştır (www.ödevsitesi.com).
Yağ çıkarma işleminde kaplanacak parçaların yüzeyinde bulunması muhtemel yağ tabakasının kaldırılması lazımdır, aksi halde çöküntü yapışık olmaz.
Bir organik yağ bahis konusu ise, bir bazla sabunlaştırılır; husule gelen sabun çözünür. Mineral yağlar sabunlaşmazlar, bunlar başka vasıtalarla çıkarılırlar. Yağlar üç metodla çıkarılır. 1) organik çözücülerle ; 2) alkali çözeltilere batırmakla ; 3) elektrolitik olarak. Birinci metodda organik çözücü kullanılır. Parçayı eter, benzin yahut karbon tetraklorüre batırmak kafidir. Şimdiki halde buharla yağ çıkarma çok geçerlidir. Parça derin bir silindirik kapta elektrik tertibatı ile kaynatılan çözücü buharları içine asılır, buharlar parça üzerinde yoğunlaşır ve yağ çözünüp akar, bir kaç saniye içinde temizleme tam olur. En uygun çözücü etilen triklorürdür (C2HCI3). İkinci metodda yağlar sıcak alkalilerle sabunlaştırılıp yıkamakla çıkarılır. Bu metodda alkali olarak sodium hidroksid, sodium karbonat yahut sabun kullanılır. Bu maksat için piyasada ticari isimler altında hususi olarak hazırlanmış tertipler vardır. Bunlar umumiyetle Na2CO3, NAOH, Na3PO4, 12H2O, Na2SiO3, NaCN, Na2B4O7, maddelerinden iki veya daha fazlasını ihtiva eder. Elektrolitik olarak yağ çıkarmada temizlencek parça sıcak bir alkali çözeltisi ihtiva eden elektrolizörde ekseriya katod, nadiren de anod olarak kullanılır. Elektrolitik dekapajda çözeltinin bileşimi Na2CO3 50 g/litre, NaCN 10 g/litre dir (www.ödevsitesi.com).
Yağ çıkarmanın tam olduğundan emin olmak için su ile deneme yahut morötesi ışıkla fluoresans denemesi yapılır.
Oksid tabakasının kaldırılması (dekapaj) yağdan temizlenmiş olan metalik parçalar daima ince bir oksid tabakasiyle kaplıdır. Bu tabakanın kaldırılması lazımdır. Demir ve çeliğin dekapajı için umumiyetle 2N HCI veya H2SO4, döküm parçaları için % 1-1,5'luk HF, bakır alaşımları için bir H2SO4 ve HNO3 ve çok az miktarda HCI karışımı kullanılır. Bazen biraz is ilave edilir (daha düzgün bir etki için). Elektrolitik yolla dekapajda parça bir H2SO4 çözeltisinde katod olarak kullanılır ; mesela demir ve çelik halinde 60°C da % 30'luk H2SO4 çözeltisiyle elektroliz yapılır (http://www.odevsitesi.com/odevler/2005).
Oksit tabakasının kaldırılmasından sonra temizlenen parçalar bol su ile yıkanır. Parçalar parlak görünüşlü olmalı ve her yeri su ile ıslanmış bir şekilde olmalı.
3.2.1.2. Banyoda Kaplama
Kaplanacak parça bundan evvelki işlemlerden sonra elektroliz kabına konulup derhal akım geçirilir. Aksi takdirde yeniden bir oksid tabakası husule gelebilir. Aynı sebepten kaplama işleminin aralıksız devam etmesi lazımdır. Uygulama sona erdikten sonra parça banyodan çıkarılır, soğuk su ile bolca yıkanır ve kaynamakta bulunan suya daldırılır ve burada sıcaklığı alması beklenir. Parça üzerindeki rutubeti almak için ince odun talaşı içine sokulup kurulanır veya bazen etüve konur.
3.2.1.3. Perdahlama Cilalama ve Mat Parlatma
Perdahlama ve cilalama işleminde son kademe olarak parçalar deri veya bez yahutta keçe fırçalarla parlatılır.
Mat parlatmada da isteğe bağlı olarak parçalar bez ile çok iyi parlatıldıktan sonra dekoratif amaçlar için matlaştırılabilir. Bunun için polüretan bağlantılı çok ince tane iriliğinde üretilmiş disk veya blok halindeki aşındırıcılar kullanılır (http://www.odevsitesi.com/odevler/2005_10/152318-elektroliz.htm ).
3.2.2. Galvanizin Kalitesine Etki Eden Faktörler
Galvanizin kalitesine etki eden faktörler arasında akım yoğunluğu, konsantrasyon karıştırma, sıcaklık, uygulamanın şekli, kolloidler, ph etkisi, kaplamanın dağılma gücü gibi etkiler vardır.
3.2.1.1. Akım Yoğunluğu
Akım yoğunluğu artışının çöküntünün yapısı bakımından iki zıt tesiri vardır. Akım yoğunluğu artınca billurların oluşma hızı artmış olur ve çöküntü ince yapılı olur. Fakat akım yoğunluğu daha da artınca katod dolayında deşarj olan metal ionlari çözelti içinden gelenlerle karşılanamadığından katodda bir fakirleşme meydana gelir ve bunun neticesi kaplama homojen olmaz ve fena kaliteli olur. Siyah ve süngerli kaplamalara yanmıştır denir. Katodda hidrojen yayılımı akım yoğunluğunun artmış olduğuna işarettir. Kaplama esnasında akım yoğunluğu devreye yerleştirilen bir ampermetre ile kontrol edilir.
3.2.1.2. Konsantrasyon Karıştırma
Kaplamanın yapısı üzerinde konsantrasyonun etkisi büyüktür. Billurların oluşum hızı büyük olacağından ince yapılı yapışık bir kaplama elde edilir. Katoddaki mevzii fakirleşmeyi karşılamak maksadiyle banyonun karıştırılması faydalıdır. Bundan başka, katodda toplanmış olan gazlar koparıldığı gibi kendiliğinden de bir polisaj sağlanır. Öte yandan, karıştırma kaplama gücünü azalttığı gibi, çamur ve sairenin banyoda süspansiyon halinde kalmasına sebep olur ve kaplamanın kalitesini bozar. Bu sebepten banyoyu arada sırada süzmek lazımdır.
3.2.1.3. Temperatur (Sıcaklık)
Temperaturun iki zıt etkisi vardır. Bir taraftan diffusyonu artırdığından billurların oluşum hızını artırır ve böylece küçük billurlu yapılar elde edilir. Fakat öte taraftan katod polarizasyonunu azaltır ve böylece büyük billurların oluşumuna ve bunların büyümesine sebep olur. Ayrıca hidrojen aşırı potansiyeli de azalacağından hidrojen yayımı kolaylaştırılmış olur ve kaplama süngerli olur.
Orta temperaturlarda birinci etki, yüksek temperaturlarda ikinci etki kendini gösterir. Uygununu deneme ile bulmak lazımdır. Bununla birlikte sanayide çok kere sıcak banyolar kullanılır. Çünkü 1-) metalik tuzların çözünürlüğü artacağından derişik çözeltilerin kullanılması mümkün kılınır; 2-) iletkenlik artar; 3-) toplanmış hidrojen miktarı azalır ve böylece demir ve nikel halinde kopabilen kaplama önlenmiş olur.
3.2.1.4. Uygulamanın Şekli
Kompleks tuzların elektroliziyle elde edilen kaplamaların normal tuzlarla elde edilenlerden üstün nitelikte olduğu çok eskiden beri bilinen bir özelliktir. Hususiyle Cu, Ag ve Au kaplamalar bu metallerin potasium siyanur çift tuzlarından elde edilir.
Az olmakla beraber, ikinci ionlaşma neticesi katod civarında az miktarda Ag+ ionları bulunur ve bunlar K+ ionlarına nazaran tercihan deşarj olurlar. Siyanür banyolarında An ve Cu ın ayrılması da aynı mekanizma ile olur. Gümüş halinde basit çözeltilerle uzun iğneli ve az yapışık bir kaplama, halbuki siyanür çözeltilerle beyaz, gayet yapışık, küçük billurlu bir kaplama elde edilir. Kompleks tuzların elektrolizinde basit tuzların elektrolizine nazaran katod polarizasyonu daha fazla olur, yani daha yüksek bir potansiyel tatbik edilir ve bu da taneciklerin oluşumunu kolaylaştırmış olur (http://www.odevsitesi.com).
Bir başka önemli nokta da hidrolis neticesinde kolloidal cisimler meydana gelmesidir ki bunun iyi kaliteli kaplama elde etmede tesiri büyüktür. Bundan başka, katod civarındaki fakirleşme basit tuz halinde kompleks tuz halindekinden daha fazladır.
3.2.1.5. Kolloidler
Kaplamaların kalitesini artırmak için banyoya jelatin, zamk gibi kolloidlerin ilavesinin iyi olduğu çok eskiden beri bilinmektedir. % 0,05 g/litre ilave kafidir, fazlası kaplamayı bozabilir. İlave cisim olarak jelatin, pepton, agar agar, tutkal, çeşitli zamklar, kauçuk, kazein, alkaloidler, boyar maddeler, şekerler kullanılır ; bu cisimlerin hemen hepsi kolloid yahut redüktordur. Bunlar umumiyetle yüzey aktif cisimdir, billur zerreleri üzerinde absorplanıp büyümelerini önlerler ve böylece küçük billurlu yapılar elde edilir.
Nikel ; klorür ve sülfat çözeltilerinden kolloid cisim ilave edilmediği halde de düzgün yapılar verir. Çünkü nikelle birlikte biraz hidrojen de ayrıldığından katod civarında elektrolit etkisi olur ve kolloidal olan bazik bir tuz meydana gelir ki bu da kaplamanın düzgün olmasını sağlar (www.odevsitesi.com).
3.2.1.6. pH etkisi
Kaplama çözeltileri a-) asid, b-) neutral ve c-) alkali olmak üzere üçe ayrılır.pH ye göre ise a-) pH<2 b-) 2<pH<8 ve c-) pH>8 dir. Mesela a sınıfına asid bakır ve krom banyoları ; b sınıfına nikel banyoları, c sınıfına da çeşitli metallerin siyanür çözeltileri girer. Kaplamalarda pH tayini önemlidir.
3.2.1.7. Kaplama Dağılma Gücü
Kaplamacılık bakımından kaplamanın sadece görüntüsünün ve özelliklerinin istenilen şekilde olması yeterli değildir. Aynı zamanda kaplamanın eşyanın her tarafında aynı kalınlıkta olması da lazımdır. Ekonomi bakımından kaplamanın minimum kalınlıkta olması istenir. Tatbikatta kaplanan eşya genellikle düzgün olmayan bir biçim gösterir. O halde her noktanın mümkün olduğu kadar aynı kalınlıkta olmasın çalışmak lazımdır. Yoksa tabaka kalkabilir.
Düzgün olmayan şekilli bir katod üzerinde oldukça düzgün bir kaplamanın elde edilmesi için çözeltinin gösterdiği özelliğe dağılma gücü denmiştir. Bu anlam kaplama gücü terimiyle daha iyi ifade edilebilir. Son yıllarda dağılma gücü esas itibariyle kaplama dağılımının, yani eşyanın muhtelif kısımlardaki kaplama kalınlığının bir ölçüsü olarak kullanılmaya başlanmıştır. Pratikte bu iki terim birbirine sıkı surette bağlıdır. Düzgün olmayan bir biçime sahip olan bir katod kaplanmak istendiğinde anoda yakın olan kısımlar daha uzaktakilere nazaran daha kalın bir tabaka ile kaplanırlar. Çünkü Ohm kanununa nazaran yakın noktalar arasında direnç daha azdır. Ohm kanununun tatbikiyle hesaplanan dağılıma akımın primer dağılımı denir. Bir çok çöküntülerde eşitsiz şekildeki bir çökme temayülü, daha düzgün bir kaplama sağlamaya çalışan diğer faktörlerle karşılanır. Ohm kanununun tam tatbikiyle elde edilecek gayri muntazam dağılımı tabii surette düzeltebilen bir elektrolitik çözeltiye iyi kaplama güçlü çözelti ; Ohm kanununa göre kaplama hasıl eden çözeltilere de kaplama güçlü olmayan çözelti denir.
Anoda yakın olan bir nokta öteki noktalara nazaran daha yüksek bir akım yoğunluğuna tabi tutulduğunda bir süre sonra bu nokta metalik ion bakımından fakirleşmiş olur ve bir polarizasyon kendini gösterir ve bir zıt E.M.K. meydana gelir ki bu düşünülen nokta ile anod arasında elektrolit direncinin artmasına tekabül eder. Bunun neticesi anoda uzak olan noktalar hesabın gösterdiğinden daha büyük bir akım alır ve böylece kaplama gücü artar. Eğer polarizasyon meydana gelmemiş olsa anoda yakın noktalar daha çabuk kaplanır ve gittikçe anoda daha da yakınlaşmış olacağından neticede kaplama saçaklı olur. Çözeltinin iletkenliğininin fazlalığı oranında polarizasyon fazladır. O halde yüksek iletken çözeltilerde kaplama gücü fazladır. Temperatur artışı iletkenliği arttırırsa da polarizasyonu daha fazla azalttığından kaplama gücünü azaltmış olur (www.odevsitesi.com).
SONUÇ
İnsanlar en eski çağlardan başlayıp günümüze kadar olan tüm zamanlarda doğaya karşı hep bir mücadele içinde olmuşlardır. Bu mücadelelerden biride korozyon (aşınma) dır.İnsanlar metalleri aşınmalara karşı korumak için galvanizi kullanmışlardır.
Zamanla ve teknolojinin gelişmesiyle galvaniz koruma amaçlı kullanılmaktan çıkıp değişik alanlarda farklı nedenlerle kullanılmaya başlanmıştır. Tezde bu alanlardan biri olan kuyumculuk alanında kullanılan galvaniz konusuna değinilmiştir.
Kuyumculukta kullanılan galvaniz işlemleri sayesinde kaplanan metal aşınmalara karşı korunmakla kalmayıp; metalin değerinin artmasını da sağlamaktadır. Özellikle metalin ekonomik değerini yükseltecek kendisinden ileri bir soy metalle yüzeyinin belirli kalınlıklarda kaplanması galvanizin, kuyumculuk alanında aşırı derecede kullanılmasını olanak sağlamaktadır.